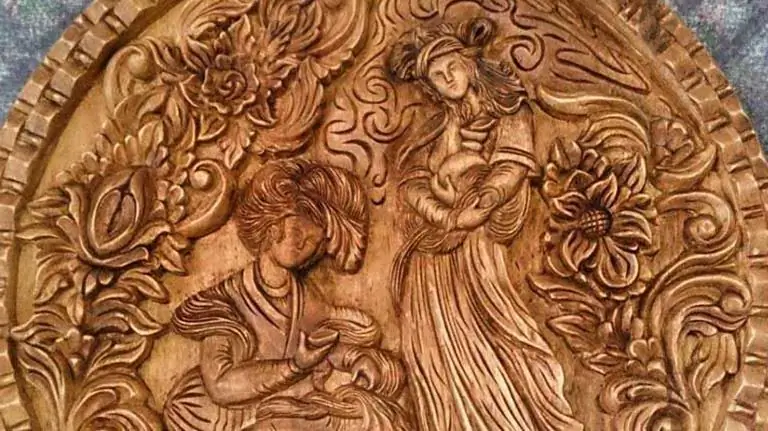
Inhaltsverzeichnis:
2025 Autor: Sierra Becker | [email protected]. Zuletzt bearbeitet: 2025-06-01 05:43
Holzschnitzerei ist sicherlich eines der ältesten Handwerke, die die Menschheit je ausgeübt hat. Auf diese Weise lassen sich Geschirr, Gebäudeteile, Möbel, Truhen, Backgammonkisten usw. dekorieren, Holz schnitzen kann natürlich jeder lernen. Die Hauptsache ist, die richtigen Werkzeuge und Rohlinge auszuwählen und die erforderlichen Techniken zu beherrschen. In diesem Fall wird das Holzschnitzen für einen unerfahrenen Handwerker bald zu einem Hobby, das nicht nur angenehm ist, sondern vielleicht sogar ein gutes Einkommen bringt.
Thread-Typen
Es gibt vier grundlegende Techniken, um Holzprodukte auf diese Weise zu dekorieren:
- durch;
- taub;
- skulptural;
- Haus (Schiff).
Skulptarisches Schnitzen wird über das gesamte Volumen des Werkstücks durchgeführt. Das Endprodukt ist in diesem Fall eine separate Figur oder eine dreidimensionale Komposition. Diese Art des Schnitzens gilt als ziemlich schwierig und ist eher für erfahrene Handwerker geeignet.
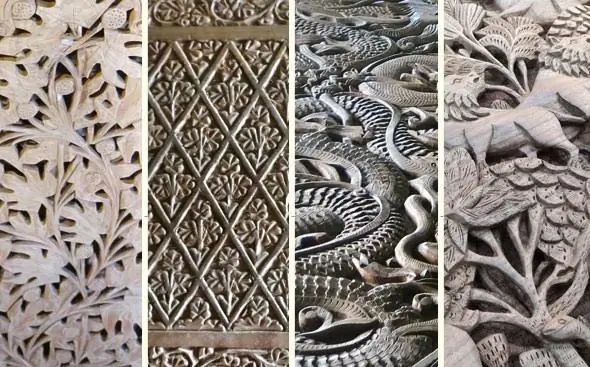
Hausschnitzerei, auch Schiffsschnitzerei genannt, kombiniert Elemente aller anderen Techniken und wird verwendet, um Gebäude und Strukturen zu schmücken. Mit dieser Technologie können beispielsweise Platbands, Baluster und Geländer von Treppen, Firste von Hausdächern usw. geschnitten werden. Für einen Anfänger ist diese Technik nicht schlecht, da sie sich nicht durch zu große Komplexität unterscheidet.
Through-Thread
Diese Technologie wiederum wird klassifiziert in:
- Schlitz;
- durchbrochen;
- propyl.
Die End-to-End-Technik zeichnet sich vor allem dadurch aus, dass die Produkte bei ihrer Anwendung keinen Hintergrund haben. Solche Technologien werden am häufigsten für die Herstellung von Architraven oder beispielsweise bei der Gest altung von Holzkirchen verwendet.
Alle drei Arten von durchgehenden Fäden sind technisch sehr ähnlich. Der Unterschied zwischen ihnen liegt nur im Grad der Komplexität der Arbeit. Die einfachste Art von Durchgangsgewinde ist ein Sägegewinde. In diesem Fall wird das Werkstück ohne weitere Ausarbeitung der Details entlang der Konturen des aufgebrachten Musters geschnitten.
Produkte in durchbrochener Technik werden auf fast die gleiche Weise hergestellt. Das einzige ist, dass die Schnitzerei in diesem Fall durch zusätzliche kleine Details reicher aussieht.
Der geschlitzte Faden wiederum ist dem durchbrochenen sehr ähnlich. Beim Einsatz dieser Technologie wird jedoch unter anderem eine gründliche Untersuchung kleiner und großer Teile von Produkten durchgeführt. Mit dieser Technik werden unter anderem häufig Verkleidungen für Möbel hergestellt.
Zur End-to-End-Methodikman kann auch eine solche Art der Bearbeitung wie das künstlerische Sägen von Holz mit einer Handstichsäge einbeziehen. Mit dieser Technologie können Sie sehr schöne Produkte erh alten: Schachteln, Möbelbezüge, Spielzeug, Souvenirs usw. Diese Methode wird jedoch meistens nicht auf Holz, sondern auf Sperrholz angewendet.
Blinder Faden
Diese Technik wird oft zum Dekorieren von Geschirr, Möbeln, Hauswänden usw. verwendet. Das Blindschnitzen wiederum wird eingeteilt in:
- flach gezahnt;
- geprägt.
Es wird angenommen, dass das Schnitzen in Holz mit der Flachkerbtechnik am besten für Anfänger geeignet ist. Eine solche Technik kann wiederum sein:
- Umriss;
- geometrisch;
- Klammer.
Im ersten Fall werden Holzschnitte mit einem Fugenmesser, Stemmeisen mit kleinem Durchmesser oder Ecken ausgeführt. Der Kontrast zwischen Muster und Hintergrund bei Produkten mit dieser Technik wird durch Beizen erzeugt.
Geometrische Holzschnitzereien ermöglichen es Ihnen, sehr schöne Produkte herzustellen. Es ist diese Technik, die am häufigsten von Anfängern gewählt wird, die sich entscheiden, ein solches Handwerk zu beherrschen. Geometrisches Schnitzen wird normalerweise mit Werkzeugen wie einer Fahne (Beil), halbrunden Meißeln, Ecken und Pfostenmessern durchgeführt. Das Dreieck wird zum Hauptmuster beim Schnitzen mit dieser Technologie.
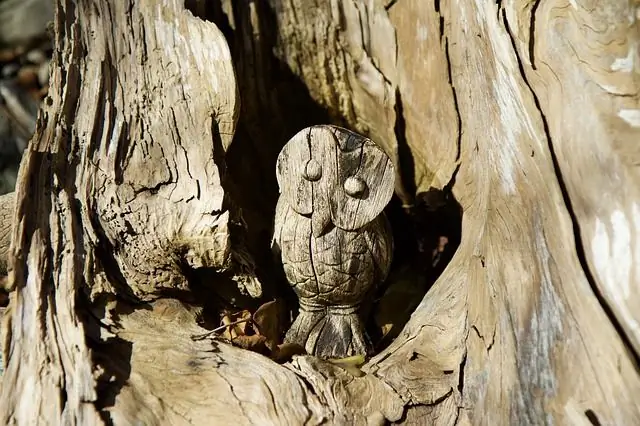
Bei gehefteten Gewinden werden nur flache Schnitte an der Werkstückoberfläche ausgeführt. In diesem Fall führt der Master vertikal durchStiche mit einem Meißel und dann - der eigentliche Schnitt. Diese Technologie der Holzschnitzerei ist die älteste. Es wurde einst von Dorfhandwerkern häufig verwendet.
Reliefholzschnitzerei wiederum geschieht:
- flaches Relief;
- Flachrelief;
- Hochrelief.
Techniken zum Ausführen der Handlung sind in diesem Fall ebenfalls ähnlich. Wenn Sie jedoch die erste Technik aus der Liste verwenden, ist das Bild ziemlich flach. Der Hintergrund bei Verwendung der Flat-Relief-Technologie kann sein:
- gepolstert - zum Bild hinabsteigen, sodass es in das Objekt gedrückt aussieht (wie ein Fußabdruck auf einem Kissen);
- oval - verkleinert (das Bild selbst wird schräg zum Hintergrund abgeschnitten).
Bei Verwendung der Basrelief-Technologie wird der Hintergrund stark reduziert. Gleichzeitig sehen die Elemente der Zeichnung selbst halbvolumig aus. Die Hochrelieftechnik gilt als noch komplexer. In diesem Fall wirkt das Bild bereits dreidimensional - fast skulptural.
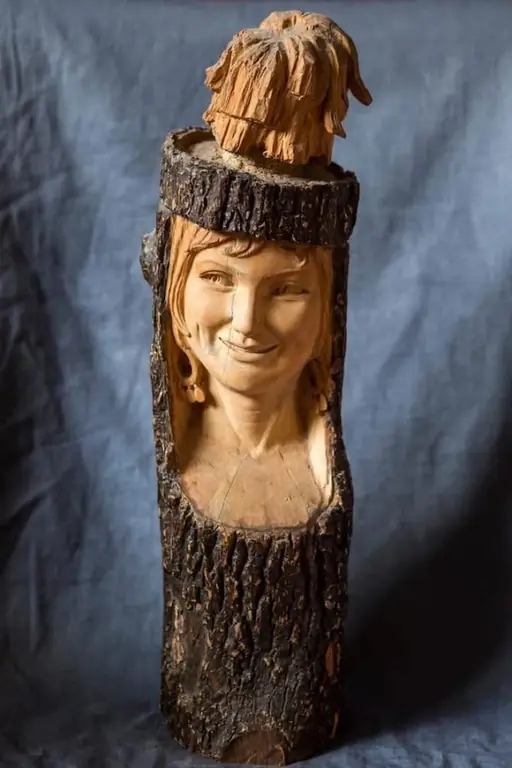
Grundlegende Tools
Am häufigsten wählen daher unerfahrene Meister die geometrische Technik mit flacher Kerbe zum Schnitzen auf Holz. Tools In diesem Fall verwenden Anfänger normalerweise Folgendes:
- Flagge (Beil);
- corner;
- halbrunde Meißel.
Ein Fahnenschneider hat eine Klinge in Form eines meist gleichseitigen Dreiecks. Gleichzeitig wird es am Griff befestigtfür die Spitze. Ein solcher Cutter markiert die Konturen von Zeichnungen, gerade Linien beim Verzieren von Seiten usw.
Die Messerecke hat vom Ende her (im Schnitt) eine V-Form. Es wird verwendet, um das Relief der entsprechenden Konfiguration zu durchschneiden. Halbrunde Meißel am Ende haben die Form eines Halbkreises. Sie können zum Beispiel zum Schneiden von glatten Kerben-Blütenblättern verwendet werden. Und Ecken und Halbkreismeißel können unterschiedliche Größen haben.
Es gibt viele andere Werkzeuge, die die Arbeit mit Holzschnitzereien erleichtern und Zeichnungen komplexer und schöner machen können. Dies können zum Beispiel Fugenmesser, gewöhnliche gerade Meißel usw. sein.
Neben dem eigentlichen Schneidwerkzeug muss sich ein unerfahrener Meister zum Schnitzen von Holz unbedingt allerlei Hilfsmittel anschaffen. Für das Design von Produkten mit geometrischer Technologie benötigen Sie beispielsweise auf jeden Fall: Zirkel, Lineal, Maßband, Winkelmesser.
Im Angebot sind heute auch Maschinen zum Schnitzen von Holz. Solche Werkzeuge werden anders Graveure genannt. Solche Vorrichtungen, obwohl sie ziemlich teuer sind, ermöglichen es, das Design von Holzprodukten zu erleichtern und zu beschleunigen.
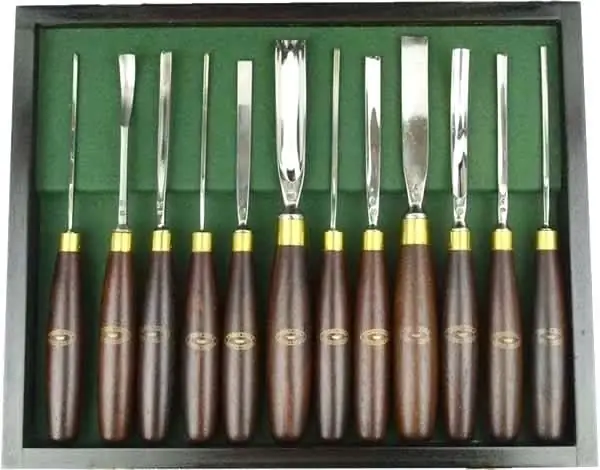
Welches Handwerkzeug für Holz kaufen: Hersteller
Am häufigsten verwenden Schnitzer-Anfänger bei ihrer Arbeit Tatjanka-Messer. Zu den Vorteilen der Werkzeuge dieses Herstellers zählen vor allem niedrige Kosten und gute Qualität. Der Vorteil von Schneidegeräten dieser Marke ist auch die Tatsache, dass aufZähler kommen sie bereits gut geschärft. Das einzige ist, dass mit den Werkzeugen von Tatyanka in den meisten Fällen nur ziemlich weiches Material bearbeitet werden kann. Aber diese Firma beliefert den Markt direkt mit ganzen Sets für Holzschnitzereien, die speziell für Anfänger entwickelt wurden.
Cutter der tschechischen Firma Nareks haben sich auch unter Carvern einen sehr guten Ruf erworben. Solche Werkzeuge sind auch von guter Qualität und in vielen Fällen kostengünstig. Aber leider werden Nareks-Fräser nicht geschärft auf den Markt gebracht. Auf Wunsch kann ein Anfänger bei diesem Hersteller auch ein Holzschnitzset erwerben.
Welches Holz soll ich verwenden
Natürlich muss sich ein unerfahrener Meister auf der ersten Stufe für die Art des Materials entscheiden, mit dem er arbeiten wird. Die meisten erfahrenen Schnitzer raten Anfängern, Lindenholz zum Lernen zu wählen. Dieses Holz ist nicht zu hart und eignet sich gut für das Messer. Lediglich Linde gilt als nicht allzu vorhersehbares Material. Je nachdem auf welchem Boden der Baum gewachsen ist, kann dieser entweder zu dicht und dementsprechend hart genug oder umgekehrt zu locker und weich sein.
Außerdem können verschiedene Arten von Schnitzereien, auch für Anfänger, hergestellt werden aus:
- zeder;
- espens;
- Birken;
- Apfelbäume;
- Kiefern.
Gleichzeitig wird angenommen, dass Zedernholz am besten für die Herstellung verschiedener Holzarten geeignet istSouvenirs, Leuchtkästen, Schachteln usw. Produkte, die im Betrieb stark beansprucht werden, können aus diesem weichen Material nicht hergestellt werden. Sie stellen zum Beispiel keine Griffe für Messer, Äxte und Hämmer, geschnitzte Regale aus Zedernholz usw. her.
Aspen gilt als sehr gut für Anfängermaterialien. Solches Holz ist sauber geschnitten und „hält“außerdem im Gegensatz zu Zeder feine Schnitzereien gut (ohne abzusplittern). Zudem ist Espe ein weit verbreitetes und daher meist preiswertes Holz. Dieses Material hat nur ein Minus. Espe ist leider schwer zu schleifen. Bei der Durchführung dieses Vorgangs steigt auf solch „benetztem“Holz normalerweise ein Flor auf.
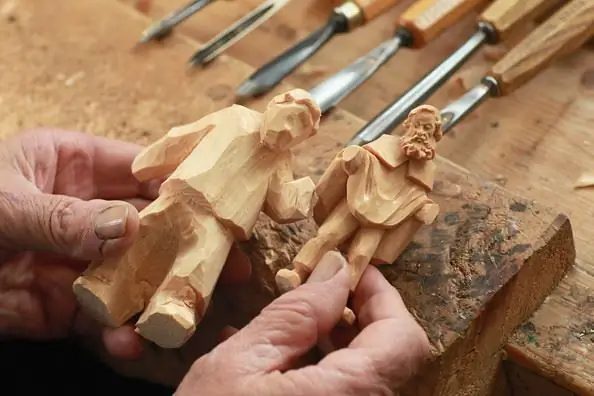
Birke ist das Lieblingsmaterial vieler Schnitzer, sowohl erfahrener als auch Anfänger. Solches Holz ist gut geschnitten, "hält" perfekt kleine Details und ist außerdem im Gegensatz zu Espe perfekt geschliffen und sogar poliert.
Die Holzstruktur des Apfelbaums zeichnet sich durch eine erhöhte Dichte aus. Daher ist ein solcher Baum für Anfänger nicht sehr geeignet. Vor dem Schneiden wird ein Apfelbaum wie eine Birke oft eingekocht. Solches Holz wird normalerweise verwendet, um Muster mit vielen kleinen Details herzustellen.
Kiefer gilt auch als Material, das sich nicht gut zum allgemeinen Schneiden eignet. Tatsache ist, dass aufgrund der gehärteten Harzadern beim Bearbeiten eines solchen Holzes mit einem Messer Späne und Hanf erh alten werden. Kiefernholz wird meistens nur für die Herstellung großer hölzerner Parkskulpturen verwendet.
Wie man ein Leerzeichen macht
Trainierebei der holzschnitzerei ist es im prinzip auf jedem kleinen holzstück möglich. Aber um ein schönes, spektakuläres Produkt herzustellen, ist es unter anderem wichtig, einen guten Rohling zu verwenden.
Wie bereits erwähnt, beschäftigen sich Anfänger meistens mit dem Schnitzen von Holz auf Linden. Um aus einem solchen Baum einen Rohling herzustellen, müssen Sie nur die Bretter selbst im nächsten Sägewerk kaufen. Solches Material sollte vorher getrocknet werden. Als nächstes müssen Sie jede Platte auf einer speziellen Maschine so schleifen, dass der Kern so gut wie möglich hervorgehoben wird.
Für die Holzschnitzerei bei der Verwendung von Linde wird nur Splintholz verwendet. Anschließend muss es mit einer Kreissäge vom Kern getrennt werden.
Lindensplint, da der Baum selbst nicht zu dick ist, meist klein. Um großformatige Platten zu schneiden, müssen solche Stäbe daher häufig verleimt werden. Das Befestigen von Kalkmaterial ist laut erfahrenen Handwerkern am besten in einem herkömmlichen Schraubstock mit dem hochwertigsten Kleber (z. B. deutscher Jowat).
Wie man Chipping vermeidet
Ein guter Satz Meißel für Holz und hochwertige Rohlinge lassen natürlich am Ende sehr schöne Produkte entstehen. Aber der eigentliche Thread selbst muss korrekt gemacht werden.
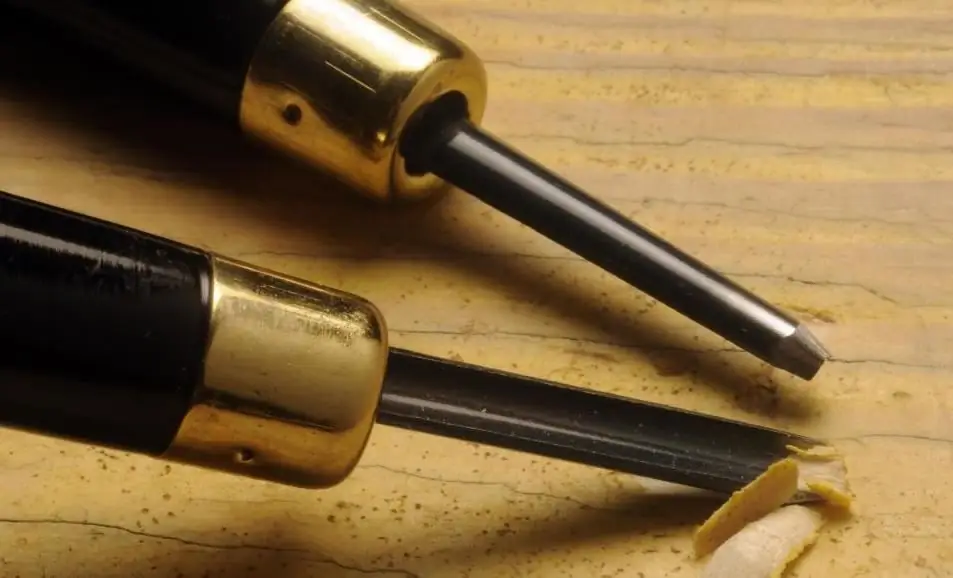
Platten - das Material ist bekanntlich faserig. Vor dem Schneiden wird ein Muster durch Pauspapier auf einen Holzrohling aufgetragen. Um Konturen und Rillen in Holz zu schneiden, müssen Sie sich in erster Linie auf die Lage seiner Fasern konzentrieren. Es ist am besten, sich an ihnen entlang zu bewegen. So ist es möglichAbplatzungen vermeiden. Unter anderem sollten Sie beim Schneiden darauf achten, dass das Werkzeug die Fasern nicht zur Seite „drückt“, sondern sich im Gegenteil in Richtung ihres Masseschwerpunkts bewegt.
Geometrisches Schnitzen
Bevor Sie mit dem eigentlichen Schnitzen unter Verwendung von Mustern, Mustern usw. fortfahren, sollte ein unerfahrener Meister ein wenig in die Arbeit mit Messern verschiedener Arten einsteigen. Mit Hilfe einer Fahne auf einer Art Trödelbrett können Sie zum Beispiel einfache schräge Schnitte, Weihnachtsbäume machen. Dann können Sie die Ecken unterschiedlich lang verwenden, gerade Schnitte machen, mit Kurven und Wellen.
Erfahrene Handwerker raten einem Anfänger, sich mit verschiedenen Ausstechformen vertraut zu machen. Sonst bekommt er später keine saubere Schnitzerei, was zu Enttäuschungen führen kann.
Wo bekomme ich Vorlagen
Schöne Holzarbeiten auf Bestellung und für den persönlichen Gebrauch können natürlich nur mit spektakulären Vorlagen hergestellt werden. Stilvolle und attraktive Schablonen zum Schneiden in unserer Zeit lassen sich am einfachsten im Internet auf spezialisierten Websites herunterladen. Darüber hinaus können Sie eine solche Vorlage natürlich auch selbst erstellen. Bei geometrischen Gewinden können Sie beispielsweise mit Zirkel, Winkelmesser und Lineal direkt auf dem Werkstück skizzieren.
Für das Schnitzen in anderen Techniken sind bei der Wahl der Schablone unter anderem folgende Regeln zu beachten:
- für die Gravur sollte die Vorlage möglichst einfach sein;
- Für ein großes Produkt sollten Sie keine Schablone mit vielen kleinen Details (undumgekehrt).
Die Linien aus der vorhandenen Schablone zum Schneiden von Holz mit einer Stichsäge oder Spezialmessern sollten möglichst genau auf das Werkstück übertragen werden. Sonst wird ein ordentliches Produkt später nicht funktionieren.
Fleckenbehandlung
In der Endphase werden geschnitzte, maßgefertigte Holzprodukte sowie solche für den persönlichen Gebrauch oft zusätzlich mit Beize oder Lack gebeizt. Diese Produkte sind dafür bekannt, dass sie dem Holz ein helleres und attraktiveres Aussehen verleihen, ohne seine markante natürliche Textur zu verbergen.
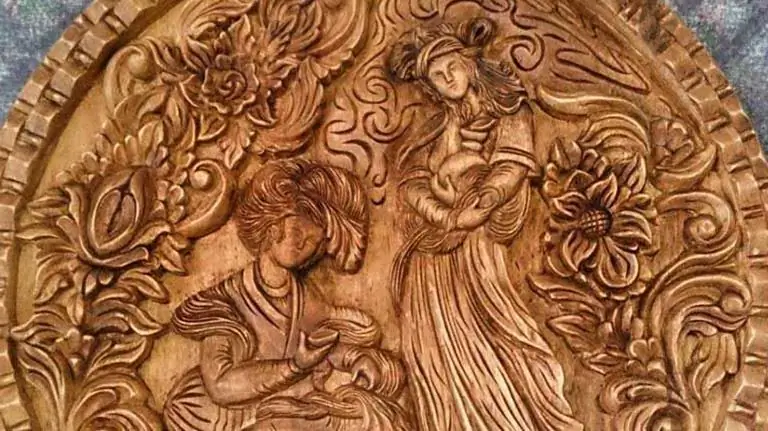
Für den gleichen Zweck kann ein moderneres Werkzeug verwendet werden - Wachs zum Polieren von Holz. Solches Material sowie Beizen und Lacke, die zum Färben von geschnitzten Produkten bestimmt sind, können unterschiedliche Farben haben. Bei Schnitzern sehr beliebt sind zum Beispiel Nuancen von Eiche, Erle, Mahagoni etc. In jedem Fall wird das Holz vor dem Beizen mit solchen Mitteln meist sorgfältig mit transparenten, farblosen Produkten grundiert.
Sehr oft werden unter anderem Schnitzereien zusätzlich ge altert. In diesem Fall werden sie mit Beize vorgestrichen und dann mit Schleifpapier geschliffen.
Empfohlen:
Quilling für Anfänger: einfaches Handwerk, Werkzeuge und Materialien

Der Artikel beschreibt ausführlich die Herstellung einzelner Elemente aus Quillingstreifen und gibt Beispiele für das einfachste Handwerk. Nach dem Lesen können diese Werke sowohl von Kindern als auch von Anfängern ausgeführt werden - Liebhaber, die mit ihren eigenen Händen etwas Besonderes, Originelles schaffen. Fantasieren Sie und setzen Sie Ihre Ideen in Handarbeit mit der Quilling-Technik um. Es ist sehr interessant und wird Sie definitiv fesseln
Wie man eine Lünette mit Bändern flechtet: Techniken für Anfänger und Beispiele mit Fotos

Wie man ein Stirnband mit Bändern verziert. Beschreibung der Techniken mit einem Tape oder zwei Tapes. Was ist die Kanzashi-Technik und wie können Sie damit das Stirnband mit Bändern flechten? Mit Blumen geschmückte Stirnbänder
Papier-Origami: Schemata für Anfänger. Origami: Farbschemata. Origami für Anfänger: Blume
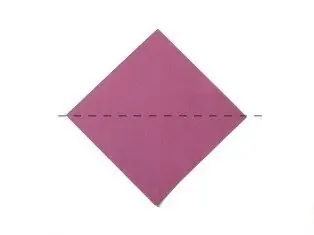
Heute ist die alte japanische Kunst des Origami auf der ganzen Welt bekannt. Seine Wurzeln reichen bis in die Antike zurück, und die Geschichte der Technik zur Herstellung von Papierfiguren reicht mehrere tausend Jahre zurück. Überlegen Sie, was ein Anfänger verstehen sollte, bevor Sie mit der Arbeit beginnen, und machen Sie sich mit einer der Möglichkeiten vertraut, schöne und leuchtende Blumenarrangements aus Papier zu erstellen
Tipps für Anfänger: wie man mit Polymer Clay arbeitet. Benötigte Materialien und Werkzeuge, Arbeitstechnik
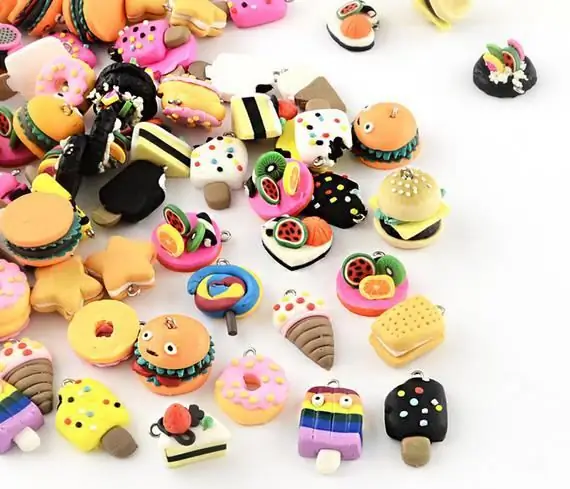
Eines der beliebtesten kreativen Materialien ist Fimo. Daraus entstehen Schmuck, Souvenirs, Spielzeug usw. Um die Technik der Arbeit mit Fimo zu beherrschen, müssen Sie den Rat erfahrener Handwerker berücksichtigen. Es gibt viele Feinheiten und Nuancen, deren Kenntnis es Ihnen ermöglicht, schwerwiegende Fehler zu vermeiden. Überlegen Sie als Nächstes, welche Meister Anfängern Ratschläge geben und wie man mit Fimo arbeitet
Rosenkranzflechten: Der Zweck des Rosenkranzes, die Technik der Ausführung, die notwendigen Materialien und Werkzeuge, Schritt-für-Schritt-Anleitungen für die Arbeit und fachmännis

Häufig gibt es im Alltag so etwas wie einen "Rosenkranz". Viele Menschen haben nicht einmal eine Ahnung, welchen Zweck dieses Attribut hat. Dieser Artikel beschreibt die Geschichte und den Zweck des Rosenkranzes und schreibt auch einen Weg, den Rosenkranz richtig zu weben