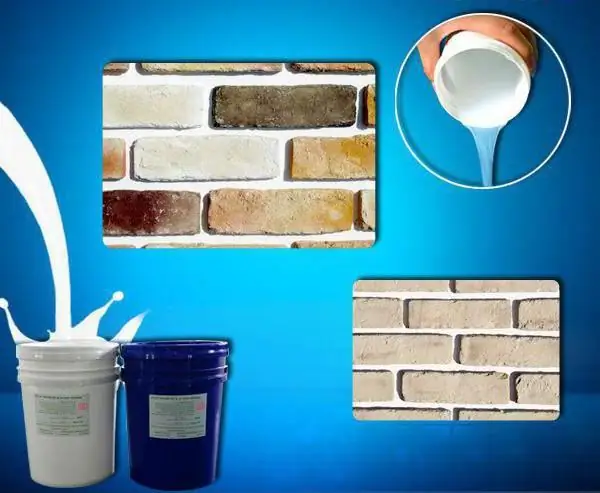
Table of contents:
2025 Author: Sierra Becker | [email protected]. Last modified: 2025-01-22 22:09
Silicone compound is an ideal material for making molds for fossils, lifecasts and other hard objects. As a liquid latex, it gives a light, flexible, high fidelity shape. It also has the added benefit of longer life and resistance to chemicals and degradation. It is the recommended material for making durable molds from important specimens. Gypsum silicone molds can be made in less time than a latex mold if "fast" catalysts are used. The only drawback is that it is more expensive than latex and is not as resilient, resulting in breakage and damage.
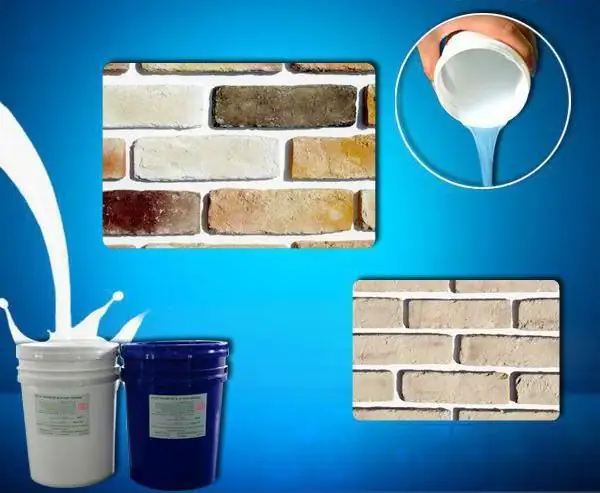
Composition of silicone material
This material consists of silicone paste as a base and a platinum catalyst that accelerates curing.
When creating molds, silicone compound is used transparent, red, yellow, white and other colors. The hardener may also have a different palette or be colorless.
After mixing the two components at room temperature, the silicone mass becomes solid and takes on a rubbery appearance. Typical curing time for most is between 18-24 hours, but curing time can be greatly reduced by using fast acting catalysts.
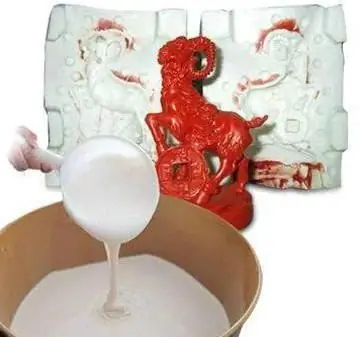
Types of silicone compounds
The most common rubber compounds used to make molds are RTV, RTV-2 and HTV. Unlike RTV (room temperature vulcanizing) rubbers, HTV silicone requires temperatures in excess of 100°C to cure.
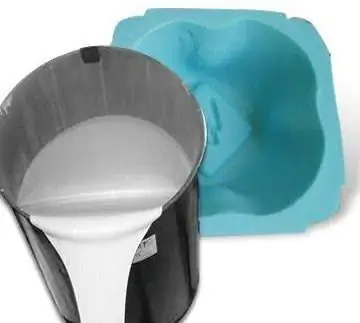
Among those who make silicone compound, everyone tries to make a variety of silicones and catalysts with different viscosities, colors and other functions.
There are two main classes of RTV silicones
1. Tin catalyzed silicones.
2. Silicones on platinum catalysts.
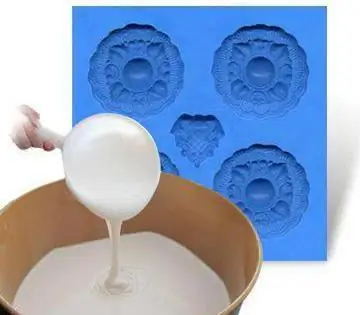
Each of them has its advantages and disadvantages. Tin-catalyzed silicones are generally cheaper and easier to use. They have a low to medium viscosity, so they flow well around the product. In contrast, platinum is suppressed by many naturally occurring compounds, in particular sulfur, tin, amines, freshly made polyester, epoxy or urethane rubber products. Even after coating the product with acrylic varnish, the silicone compound for molds onplatinum will not harden in the presence of interaction with sulfur- and tin-containing surfaces. This makes them unsuitable for many natural objects. However, once cured, they have the greatest chemical, microbiological and heat resistance and generally remain flexible for many years. In contrast, tin-catalyzed silicones tend to become brittle after a few years of use and begin to split or tear. For these reasons, silicones in the tin group are often used for low volume casting jobs. And platinum is used for important work, especially in large volumes.
Shelf life
Many silicones can be successfully used up to 5 years from date of purchase if stored properly in airtight containers in a dry, cool place. However, catalysts lose their effectiveness quite quickly, even if properly stored they are best used within a year.
Where apply
The RTV-2 silicone compound is used to make copies of various figurines. As well as art products made from polyester, epoxy resins, wax, plaster, candles, toys and soaps, etc.
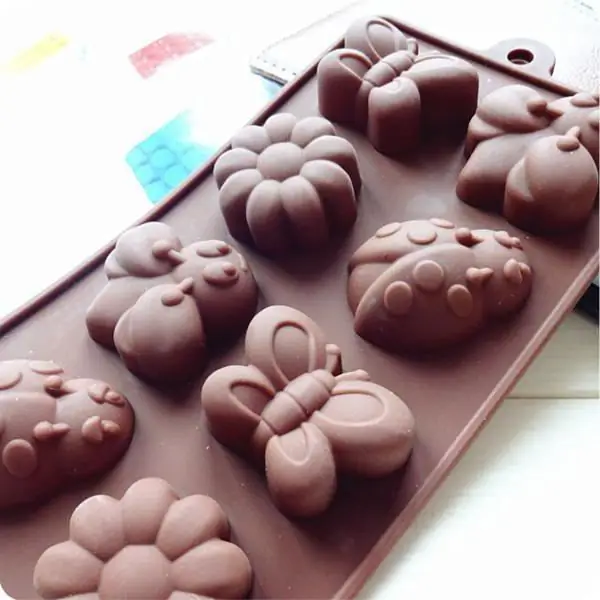
Pentelast silicone compound is food grade and safe. The advantage of this material is that it is highly flexible and does not damage the product when removed, such rubber molds can be reused. Considering that this is a food-grade silicone on a platinum catalyst, it can be used to makesilicone molds for plaster, molds for cakes and cupcakes, pastries and other confectionery.
Safety instruction
Silicone compound is a relatively safe and odorless product when used properly, however catalysts and thickeners can be toxic to eyes and skin, so these parts of the body must be protected.
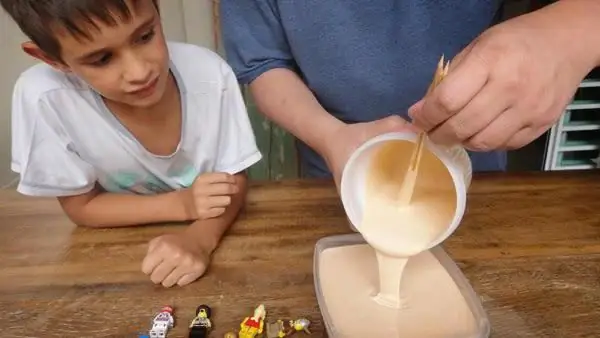
Procedure for creating molds
- The surface of the copied sample is cleaned and degreased. If necessary, use wax lubricant, soap solution or petroleum jelly.
- Material is thoroughly mixed as sediment may form during storage.
- A container is prepared in advance, in which the basis for the impression is placed. Such a container can be a plastic cup, a bottle or a box. It should have a relatively straight bottom and sides without slots or holes.
- In a clean container, the base with the hardener is diluted until a homogeneous mass is formed.
-
In order to estimate the amount of silicone required, you need to calculate the poured volume so that the product is completely covered. Another option - you can simply cover the surface of the product along with holes and depressions, after hardening pour another portion of silicone, in this case silicone and money are saved. In order to evenly coat the sample, it is desirable to pour or apply the silicone in two or more batches. The second batch is applied on top of the hardened first, but still sticky. Canalso use gauze or other reinforcing materials to be embedded between the layers, which allows you to make a more durable form.
- Catalysts are mixed in proportions depending on the type of silicone. Some of them use a base to catalyst ratio of 50:50. You can mix mechanically or manually with a spoon or stick. You can not get involved in this process for a long time no more than 2 minutes, since a long process forms a lot of air bubbles in the mixture. In order to know if a homogeneous consistency is obtained, it is better to take a colored hardener.
- After mixing, the mass is poured out as quickly as possible. The material cures to a rubbery state within 24 hours. At temperatures below +23 °C, the curing time will be longer.
Things to consider
Air bubbles can be reduced to nothing by first mixing a small part of the mixtures and using a brush to cover the sample with it. In this way, not only the annulment of bubbles is achieved, but also the clarity of the outline of the form. After applying a thin layer, leave the product alone at room temperature until the mixture is free of air and begins to harden. Then the remaining portions of the hardener are mixed with the base and applied in layers to the products until the finished form is obtained. In the laboratory, this process is easier, as it is done using machines that shake the mold and release the air. In underground conditions, you can shake by tapping on the surface yourself.
If the sample does not have naturalboundaries to prevent the silicone from flowing during pouring, a retaining wall will need to be built around the sample. This can be done with any inert material such as wood planks, clapboard, cardboard, etc. You can fix and seal the walls with adhesive tape so that the silicone does not seep through the cracks.
Attention! Certain types of silicone may slightly discolour certain types of rock that are cast. Before work, it is suggested to test and experiment with a non-essential sample before using them on valuable items.
Recommended:
Silicon paste - an assistant in creativity
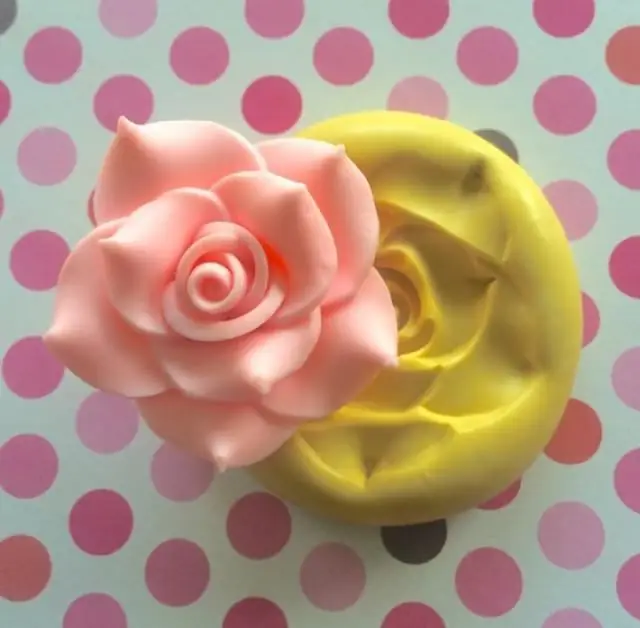
Two-component silicone paste - something that many craftswomen today find it difficult to do without. Handmade work has been valued quite highly in recent years, so there are no fewer freelancers involved in hand-made. On the contrary, their number is only growing, and the market is trying to adapt by offering products that make it easier for creators
Ukami silicone molds
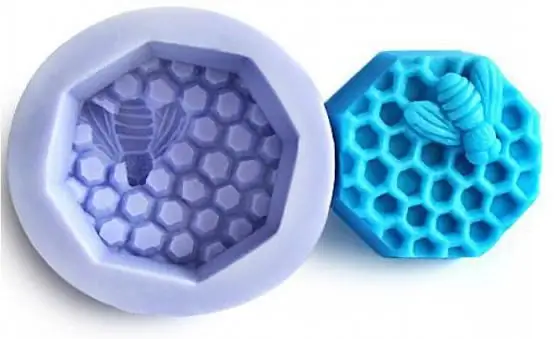
The invention of silicone has become a real godsend for hostesses. After all, excellent kitchen tools, potholders, brushes and a host of other useful devices such as oven mats are made from this material, which perfectly replace parchment paper for baking. However, modern needlewomen appreciated silicone molds most of all, with which you can easily create figurines for decorating cakes, fancy-shaped soap, candles
Making postcards with your own hands: technology, master class. Making an Easter card. Making a postcard for May 9
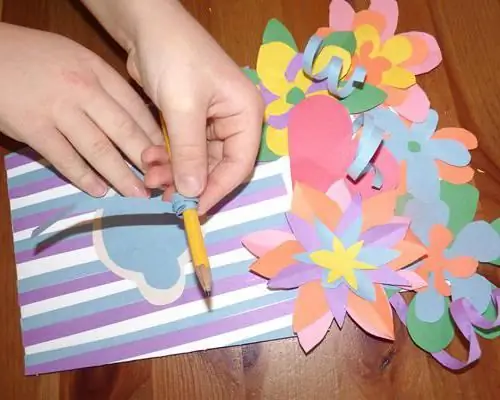
A postcard is an element with which we try to convey to a person our feelings, our mood, our festive state. Big and small, in the shape of hearts and funny animals, strict and elegant, comical and exciting - a postcard sometimes becomes much more important than the gift to which it is attached. And, of course, made with your own hands, it will bring even more joy
Decoration of the bouquet. Making bouquets of tulips. Making bouquets of fresh flowers
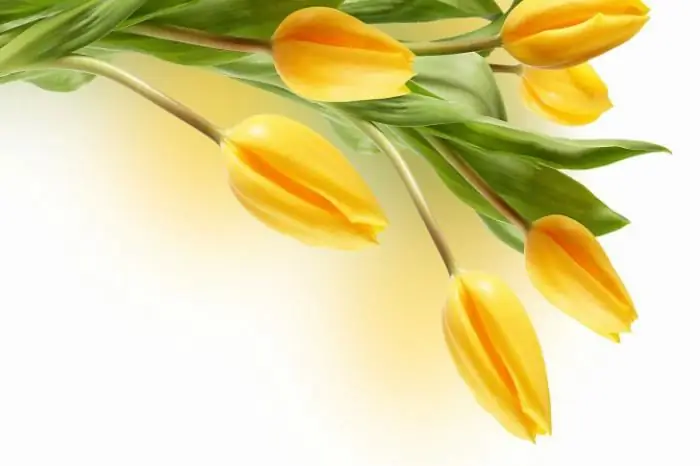
Many people love roses, chrysanthemums, orchids and gladioli, but no other flower can compare with beautiful spring tulips. Unfortunately, most often they are sold without any special decorations, simply wrapped in cellophane. But the design of a bouquet of tulips can be a truly exciting action
How to make a compound bow with your own hands
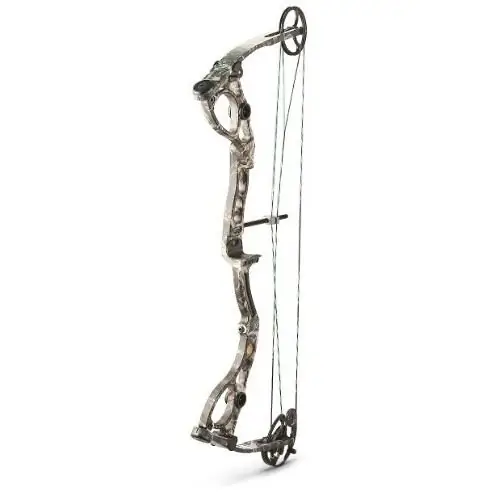
The article provides some recommendations for making a compound bow with your own hands. The characteristics of the bow and its design features are highlighted