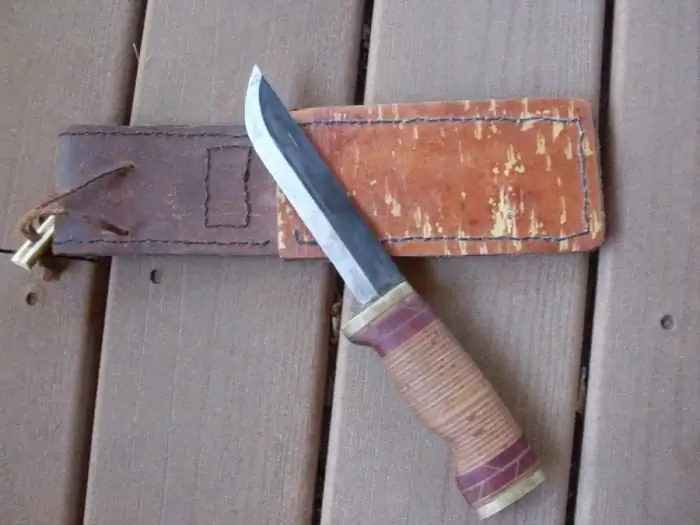
2025 Author: Sierra Becker | [email protected]. Last modified: 2025-01-22 22:09
Any self-respecting hunter has hunting knives in his arsenal, he once made them with his own hands. You can, of course, go to a specialized store and buy there, but when you do something yourself, you put your soul into it. Taking a piece of iron and turning it on a stone is not serious.
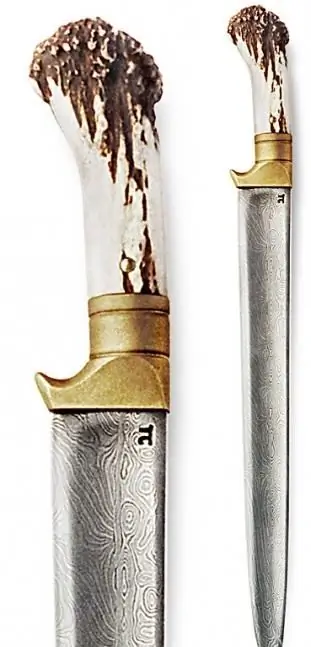
In order to make knives with your own hands, you must have a pair of hammers, different in weight, tongs with a long handle, an anvil and a horn. As experienced blacksmiths say, such a craft must begin with forging … a horseshoe. To get a hand. It makes no sense to read special literature, since it is written by professionals and for professionals, which we are not.
The rebar is perfect for our horseshoes, easy to find in a landfill or somewhere else. And besides this, it is great for studying the color of the metal during forging due to its notches. The main task is to learn how to forge iron evenly, accurately, without resorting to a file and a needle file. After passing such training, you can proceed, in fact, to the main thing - to make knives with your own hands.
Forging processtime-consuming and involves many stages, during which something new comes that captivates and interests. That is why forging is an art. Do-it-yourself knives should be made of durable steel, and 65G grade steel is best suited for this. Where can you find it? There is nowhere easier, this steel is used in truck springs. Yes, and from one spring you can make several knives, on which experiments will be carried out during hardening.
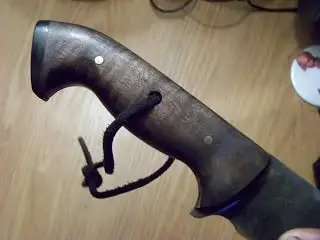
Now you can proceed to direct forging. You have already decided on the extreme color at which you can forge (reinforcing horseshoes), but it is worth remembering that steel of this brand cracks when forged at an insufficient temperature, and therefore it is better to heat it up more often. Thus, we process about 15 cm of the spring and form it into a rectangle. After that, a plate perpendicular to the spring should be forged from the rectangle. Its thickness should be slightly more than the thickness of the future knife, and 15 cm long - cut off with a chisel. In our case, we get about 10 pieces of blanks for future blades.
So, we change the big hammer to a small one, take the workpiece with tongs, warm it up and proceed to the formation of the blade contour. By the way, do-it-yourself throwing knives can be made from unsuccessful options, since they are smaller in shape and thickness of the metal. You can choose a different shape, but for a start it is better to take a classic finca as a sample.
After this, it is necessary to form the blade itself, for this the blade heats up and with light blows of the hammer is brought totrapezoidal shape. After that, it is necessary to create descents with a file or in another way without final sharpening.
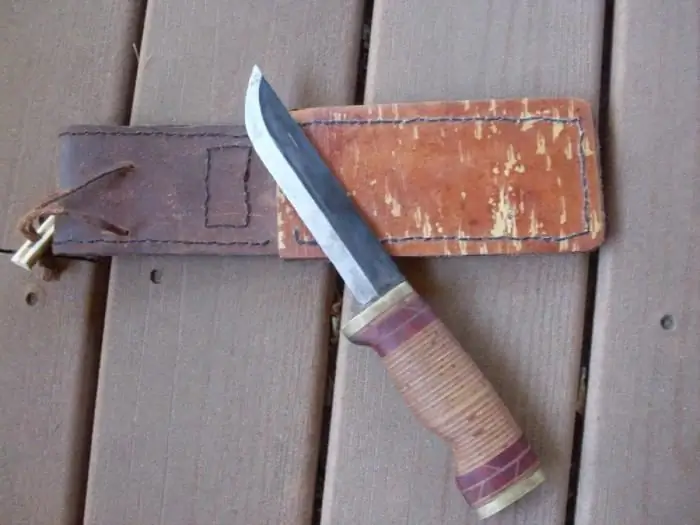
Homemade knives with their own hands, as well as in factory production, must be hardened. This is an important stage and, therefore, you should prepare thoroughly for it. To determine the desired temperature, it is required to heat each blade, while lowering the degree and throwing them into the water. Then, breaking them according to the grain size at the break, we determine the blade and the temperature with which it was heated. The blade is hardened under the same conditions, but oil acts as a coolant.
Tempering is carried out by heating it to appear yellowish in the cleaned areas and immersed in the same oil.
This is how we get the blade, but the handle is the master's business, there are no limits to the imagination and everyone can do something for themselves.
Recommended:
DIY felt pillows: ideas, patterns, manufacturing steps
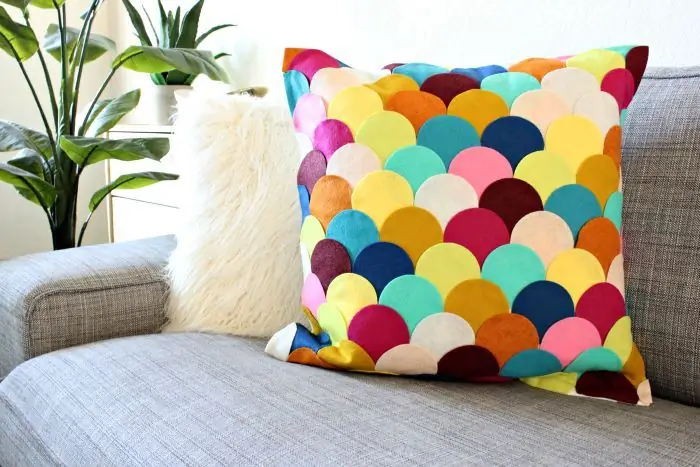
Pillows have long been used not only for sleeping, but as interior decor. They can be scattered on the sofa, near the fireplace, laid out on chairs. Many people think of the word “pillow” in their head with a picture of an ordinary square or rectangular thing stuffed with filler and with a pillowcase on top. But that hasn't been the case for a long time. In the same article, we will talk about completely different pillows, beautiful and stylish decor elements
In what state are metals best forged? What metal is better to use in forging
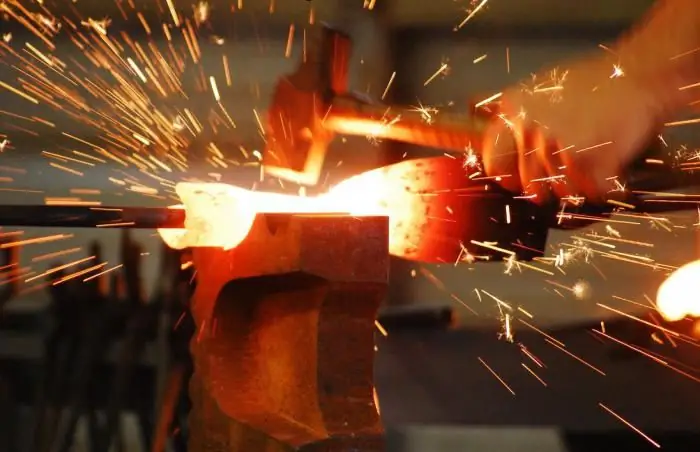
Find out in what state metals are best forged, who is a blacksmith, and what he should be, because blacksmithing is the same art as painting
Homemade knives are always held in high esteem
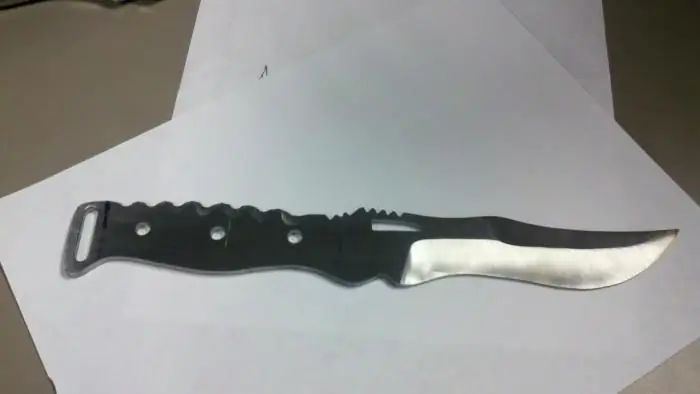
Despite the variety on the market today, homemade knives are sometimes valued higher. Often, a rather unsightly-looking handmade knife is much more convenient to hold than a product of a famous weapons company
Polymer clay - what is it? Self-hardening polymer clay
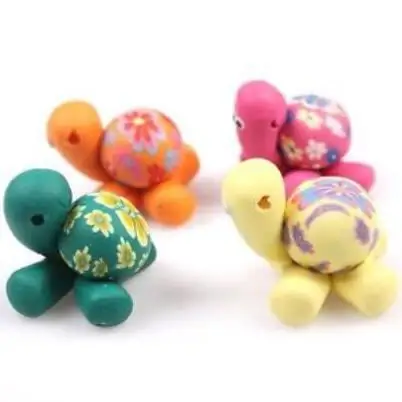
Polymer clay is an elastic material that is pleasant to work with. It is produced with different properties: one should be dried in the oven, the other is self-hardening. There are a lot of polymer clay manufacturers today, these are FIMO, Decoclay, Cernit, Kato and other companies. Having experienced different types of product, you can understand the purpose of each of them. From one it is convenient to make large figures, from the other type - small details
Self-hardening mass for modeling: step-by-step instructions for use, composition
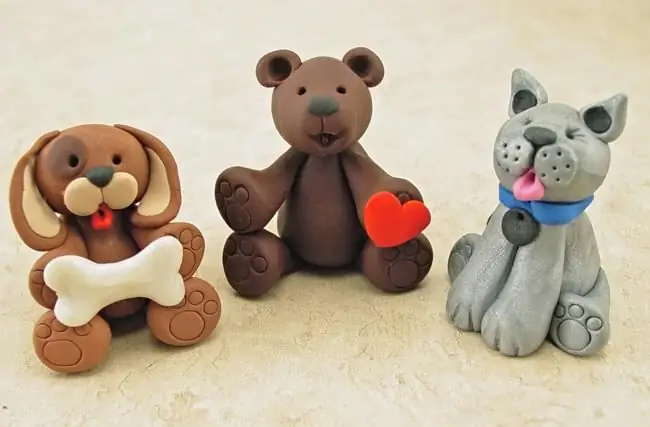
Sculpting is an exciting activity for adults and children, especially now there are many new materials. It perfectly develops children's thinking, imagination and motor skills, promotes self-expression. In addition, joint creativity brings together and helps to establish contact with other children and parents. The self-hardening mass for modeling is affordable, not in short supply, and if desired, the material can be made independently