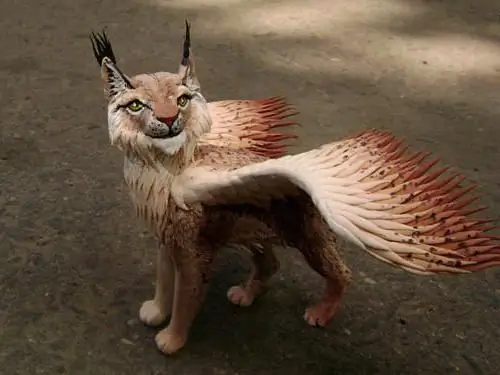
Inhaltsverzeichnis:
2025 Autor: Sierra Becker | [email protected]. Zuletzt bearbeitet: 2025-01-22 22:11
Eines der interessantesten und nützlichsten Hobbys ist das Formen von Bildern und Figuren aus verschiedenen Kunststoffmaterialien. In der guten alten Zeit stellten die Menschen Geschirr und Spielzeug aus Ton her, heute ist es durch neue, modernere Materialien ersetzt worden. Plastilin, Salzteig, Plastik, Foamiran - dies ist keine vollständige Liste. Aber heute werden wir über ein so relativ neues Material wie Samtkunststoff sprechen. Darüber hinaus werden wir sogar versuchen, es selbst herzustellen.
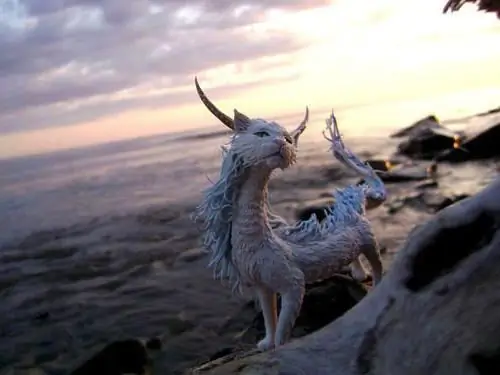
Was ist das
Ein so wunderbares Material wie Kunststoff ist seit langem in das Leben von Näherinnen und Künstlern eingezogen. Diese wunderbare Masse ist gewöhnlichem Plastilin sehr ähnlich, hat leuchtende Farben und lässt sich leicht kneten und formen. Seine Besonderheit besteht darin, dass die Plastikfiguren nach dem vollständigen Trocknen fest werden, als wären sie aus Plastik. Kunststoff hat einen erheblichen Nachteil bei der Arbeit - damit er gefriert, muss er wärmebehandelt werden: im Ofen gebacken oder gekocht. Das ist nicht immer bequem.
Velvet plastic oder, wie es auch genannt wird, Velvet Clay, hat diesen Nachteil nicht. Dies ist eine sehr leichte Kunststoffmasse, die sich angenehm anfühlt. Es trocknet von selbst an der Luft und härtet aus. Keine Hitze oder spezielle Härter erforderlich.
Samtplastik zu modellieren ist eine sehr angenehme und nicht schwierige Aufgabe. Sie müssen nur ein wenig üben. Das Material hat wunderbare Eigenschaften:
- trocknet im Freien;
- ungiftig;
- verursacht keine Allergien;
- behält nach dem Trocknen seine Form und reißt nicht;
- hat keinen starken chemischen Geruch;
- hat eine Vielzahl lebendiger Farben;
- lässt sich gut mischen;
- Klebt leicht auf sich selbst und allen rauen Oberflächen;
- schneidet gut mit Stapeln und einem Büromesser;
- kann mit verschiedenen Farben eingefärbt werden;
- erhält Schimmelabdrücke, einfach zu dekorieren;
- lackiert.
Werkzeuge
Wenn Sie sich entscheiden, mit Samtkunststoff zu arbeiten, benötigen Sie Werkzeuge. Im Prinzip unterscheidet sich das Set nicht wesentlich von dem, was beim Modellieren aus gewöhnlichem Plastilin verwendet wird.
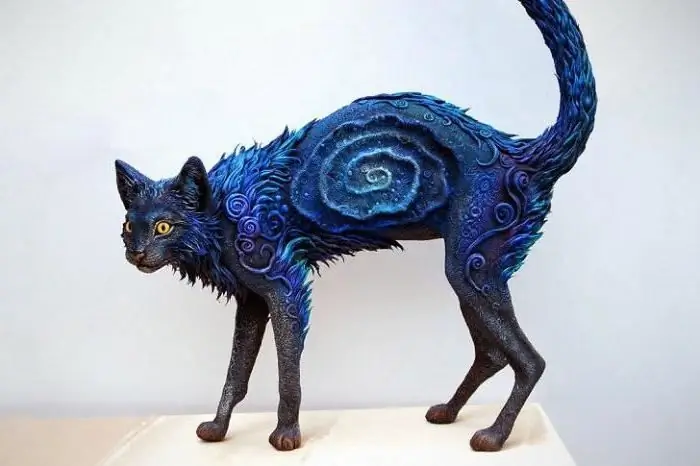
Du brauchst:
- Stapel;
- Silikonpinsel;
- Nadeln in verschiedenen Größen;
- Folie;
- Formen in verschiedenen Größen und Texturen;
- Schere;
- Glas oder Nudelholz zum Ausrollen der Masse;
- Zange;
- Kupfer- oder Stahldraht mit unterschiedlichen Durchmessern;
- verschiedene kleine Gegenstände zum Auftragen von Texturen: Spitzen, Stiftkappen und so weiter.
Erste Schritte
Bevor Sie mit der Arbeit beginnen, müssen Sie eine Skizze des zukünftigen Tieres zeichnen. Das ist sehr wichtig, es hilft die anatomischen Gegebenheiten richtig einzuschätzen und viele Details im Vorfeld auszuarbeiten.
Wenn Sie einen Draht als Grundlage für ein zukünftiges Tier benötigen, gehen Sie mit aller Verantwortung an seine Wahl heran. Aluminium sollte es zum Beispiel auf keinen Fall sein. Dieser Draht ist zu dick und locker. Bei zahlreichen Biegungen bricht es einfach. Es wird sehr frustrierend sein, wenn die fast fertige Arbeit wegen dieses Moments noch einmal gemacht werden muss.
Außerdem muss der Draht rostfrei sein, damit das Produkt lange Freude macht und nicht mit hässlichen Rostflecken übersät ist. Und natürlich die Dicke … Die Grundregel lautet: "Je größer das Modell, desto dicker der Draht." Zu dick ist es auch nicht wert, es wird sich bei Anstrengung verbiegen.
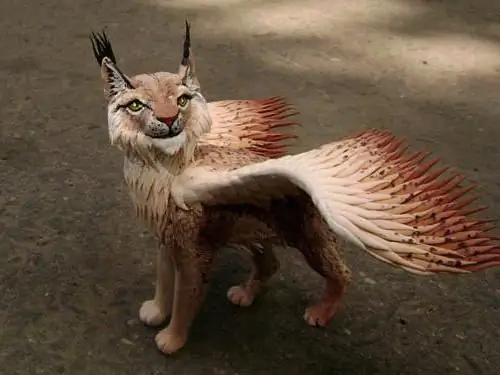
Ein Skelett erstellen
Wenn du dich entscheidest, Samtplastik zu verwenden, um ein Tier zu erschaffen, musst du zuerst ein Skelett machen. Schneiden Sie dazu drei Drahtstücke ab. Von der ersten bildet sich ein Kamm von der Nase bis zur Schwanzspitze. Aus den anderen beiden machen wir Pfoten. Damit Ihr Tier stabil steht und die Bindungen nicht auseinanderfallen, müssen die Pfoten paarweise geformt werden. Die rechte Seite wird aus einem Stück Draht geformt: Vorderpfote + Rücken. Ab dem zweiten Stück - die linke Seite. Jetzt werden alle drei Rahmen aneinander befestigt, einfach mit dünnerem Draht verdrillt. Tierbeinekann zur Stabilität leicht auseinander bewegt werden.
Gebäude "Fleisch"
Der nächste Schritt bei der Bildung des Skeletts einer Figur aus Samtkunststoff besteht darin, den Draht mit Folie zu umwickeln. Der Körper des Tieres wird daraus gebildet. Dazu werden kleine Folienstücke an den richtigen Stellen auf das Drahtgestell geklebt. Damit die Folie nicht „kriecht“, werden ihre Enden fest um den Draht gewickelt. So entsteht der Körper des Tieres, Kopf, Pfoten und Schwanz.
Am Ende sollte eine Folienskulptur auf einem Drahtrahmen stehen.
Produkt dekorieren
Jetzt ist es an der Zeit, mit dem Kunststoff selbst zu arbeiten. Wir trennen kleine Teile vom Hauptteil und beschichten die gesamte Figur damit, indem wir die Masse über die Folie streichen. Die Farbe ist in diesem Fall absolut nicht wichtig, da diese Ebene ein Entwurf ist und fast unsichtbar ist.
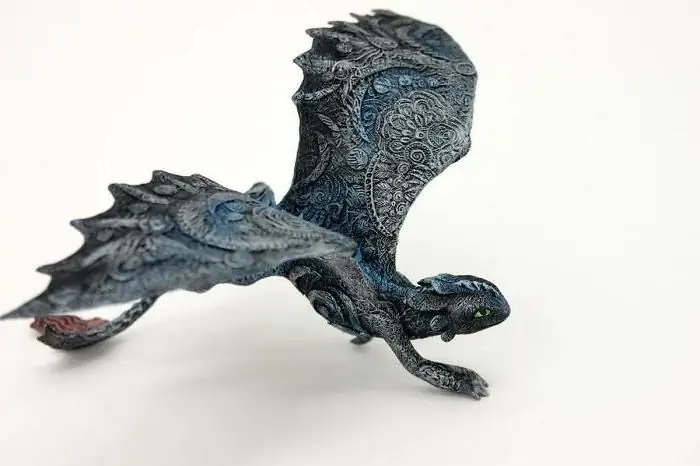
Nachdem die ganze Figur mit Plastik bedeckt ist und schon wie ein zukünftiger Märchendrache oder -bär aussieht, lässt man sie trocknen. Damit die Figur bei der Weiterverarbeitung nicht zerbricht, muss sie gut trocknen. Je nach Größe des Produkts kann dies etwa einen Tag oder sogar länger dauern.
Wenn das Produkt vollständig trocken ist, können Sie mit dem Dekorieren fortfahren. Dazu können Sie eine Vielzahl von Techniken und Tools verwenden. Um den Druck klar und schön zu machen, werden kleine Plastikstücke der gewünschten Farbe über das Werkstück geschmiert. Jetzt ist es ganz einfach, das gewünschte Muster auszudrücken oder auf eine frische Ebene zu zeichnen.
Weil Samtplastik sehr empfindlich und dünn istMaterial, dann werden daraus einfach wunderschöne Federn, Zotten, Schuppen und andere kleine Details gewonnen. Diese Arbeit ist natürlich sehr langwierig und mühsam, aber das Ergebnis ist es wert. Jede Feder oder jedes Haar wird separat hergestellt und anschließend auf das Werkstück geklebt. Es ist bemerkenswert, dass dafür überhaupt kein Kleber benötigt wird, sondern nur die Kante mit nassen Händen verschmieren.
Alle kleinen Details wie Schuppen, Federn oder Wolle werden von unten nach oben an der Figur angebracht. Das heißt, die obere Reihe überlappt leicht die vorherige. So erreichen Sie die natürlichste Komposition.
Das fertige Werk wird im Freien gründlich getrocknet und ggf. bem alt. Zum Ausmalen können Sie fast alle Arten von Farben verwenden: Acryl-, Aquarell-, Buntstifte oder Gelstifte. Das einzige, was erfahrene Handwerker zum Färben nicht empfehlen, ist Gouache. Auf Kunststoff trocknet es sehr schlecht und bleibt trotzdem klebrig. Nach vollständiger Trocknung kann das Produkt mit einem transparenten Lack überzogen werden. Dies verleiht ihm eine Art Glanz und zusätzliche Festigkeit.
Wo man lernen kann
Wenn Sie immer noch zögern, Samtkunststoff für Kreativität zu verwenden, werden Meisterkurse helfen, Ihre Zweifel zu zerstreuen. Eine davon haben wir in diesen Artikel aufgenommen. Auch wenn Sie keine geeignete Meisterklasse für die Arbeit mit Samtplastik finden konnten, können Sie die Modellierstunden von Plastilin nutzen. Es gibt einige Ähnlichkeiten zwischen diesen Substanzen.
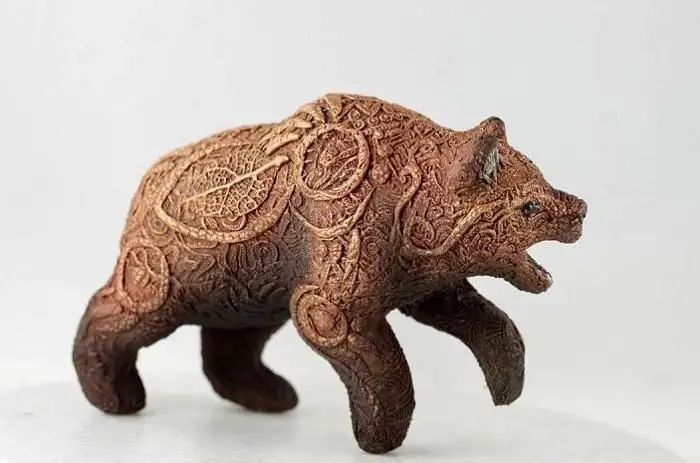
Fast alle arbeiten mit einer Substanz wie zSamtplastik, dessen Fotos in diesem Artikel vorgestellt werden, wurde vom Moskauer Künstler Evgeny Khontor aufgeführt. Der Meister verwendet dieses Material seit 2006 in seinen Werken und beherrscht die Techniken der Bearbeitung perfekt.
Wo kaufen
Da Samtkunststoff ein relativ neues Material auf dem russischen Markt ist, ist es nicht in jedem Handarbeitsgeschäft zu finden. Der beliebteste Kunststoff ist TM TUKZAR, der von Diamond geliefert wird. Der Kunststoff dieser Marke gilt als führend in Bezug auf das Preis-Leistungs-Verhältnis.
In den Geschäften des Handelsnetzes Orange Elephant können Sie A-Kleber-Modelliermasse kaufen, und in Online-Shops finden Sie Kunststoff aus Modena.
Ungefährer Preis für Samtkunststoff - 2 Rubel pro 1 Gramm. Das heißt, ein Glas mit 50 g kostet mindestens 100 Rubel. Im Allgemeinen nicht billig.
Selbsthärtendes Plastik selber machen
Da der Preis in den Läden ziemlich stark beißt, interessieren sich viele Nadelfrauen für die Frage, ob es möglich ist, Samtplastik mit ihren eigenen Händen herzustellen.
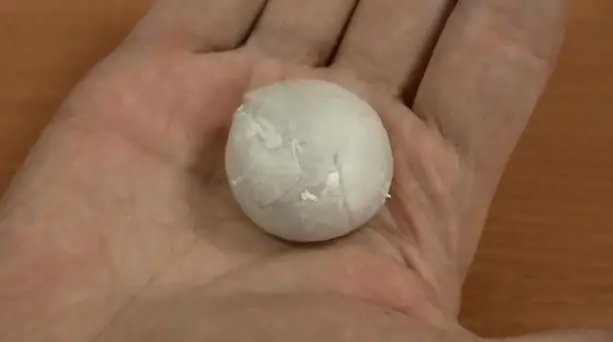
Es stellt sich heraus, dass du es kannst. Nur hier gibt es eine Nuance. Selbstgemachtes Plastik kann ziemlich giftig sein, daher ist es definitiv keine gute Idee, es kleinen Kindern zum Spielen zu geben.
Also, um Samtplastik herzustellen, brauchst du:
- kleines Glas- oder Metallgefäß;
- Aceton oder Nagellackentferner;
- Polystyrolschaum - Verpackungen aus Haush altsgeräten;
- MetallLöffel oder Pfannenwender zum Umrühren.
Gießen Sie eine kleine Menge Aceton in den Behälter und brechen Sie den Schaum in kleine Stücke. Die Teile des Schaums nach und nach in das Lösungsmittel absenken und gut mischen. Es findet eine chemische Reaktion statt, wodurch der Schaum geschmolzen und mit Aceton vermischt wird.
Wir wiederholen den Vorgang, bis sich der Schaum nicht mehr auflöst, wir handeln nach dem Prinzip "so viel wie wir nehmen". Das Ergebnis ist eine zähflüssige Masse. Jetzt müssen Sie einige Minuten warten, bis die restlichen Lösungsmitteldämpfe verdunstet sind. Denken Sie daran, dass Aceton hochgiftig ist. Versuchen Sie daher, die Dämpfe während der Arbeit nicht einzuatmen und achten Sie auf einen Augenschutz.
Um überschüssige Feuchtigkeit aus der Masse zu entfernen, kneten Sie sie zu einem kleinen Kuchen und wickeln Sie ein kleines Stück Styropor darin ein. Verschieben Sie für eine Weile. Die Masse wird sich auflösen und aufnehmen. Wiederholen Sie den Vorgang, bis sich die Stücke nicht mehr auflösen. Jetzt können Sie die Farbe der gewünschten Farbe, zum Beispiel Lebensmittel, hinzugeben und gut durchkneten.
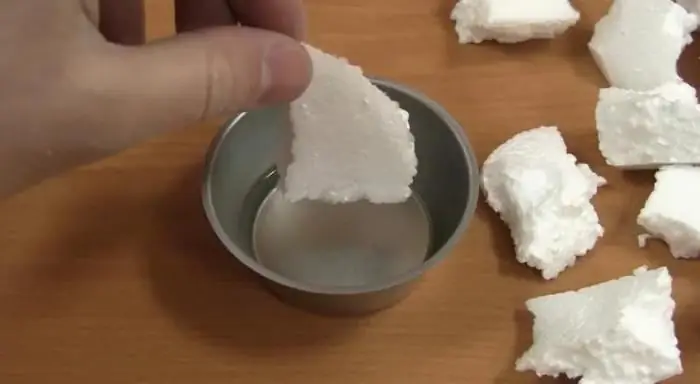
Hausgemachter Samtplastik ist fertig. Die ungefähre Zeit der vollständigen Erstarrung beträgt je nach Größe des Stücks 20 bis 30 Stunden. Wenn Sie in dieser Zeit keine Zeit hatten, es zu verwenden, legen Sie ein Stück für 4-5 Tage in Wasser. Es wird wieder weich. Die allgemeinen Eigenschaften dieses selbstgemachten Kunststoffs sind denen aus dem Laden sehr ähnlich, obwohl sie nicht genau identisch sind.
Empfohlen:
Was kann man mit Leder mit eigenen Händen machen?
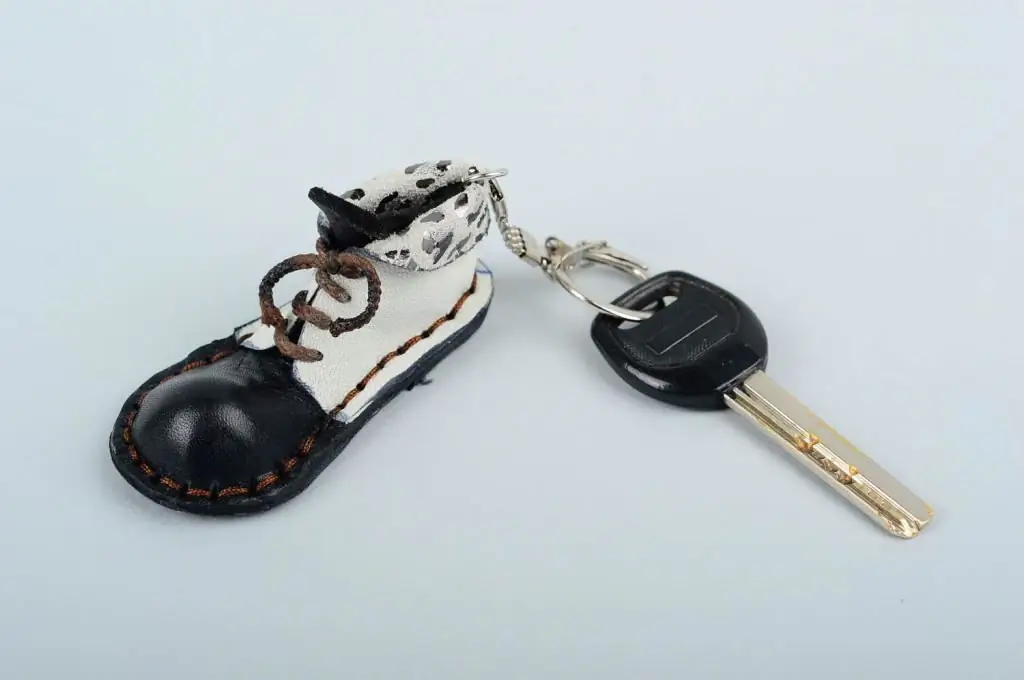
Alles Neue ist alt gut neu gemacht. Daher verwenden viele Nadelfrauen improvisierte Materialien und deren Reste, um ihre Arbeiten zu erstellen. Sie stellen sich selten die Frage, was man aus Leder, Stoff oder den restlichen Perlen machen kann. Beim Betrachten von Materialstücken blitzt mir fast sofort eine andere originelle Idee auf
Was man aus neuen und gebrauchten Patronen machen kann
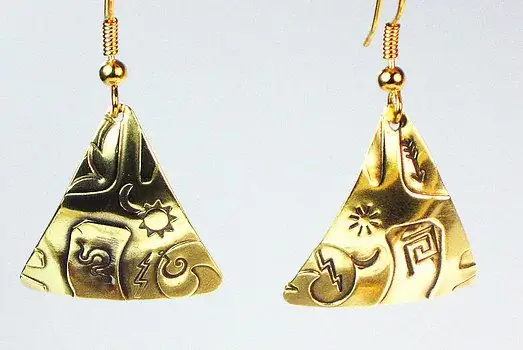
Aus verschiedenen Gründen können sich Patronenhülsen im Haus ansammeln, entweder verbraucht (nach dem Schießen) oder neu und unbenutzt. Früher konnten sie massiv in Steinbrüchen gesammelt werden. Heute sind sie auch nicht schwer zu bekommen, und einige haben sie seit mehreren Jahren und es ist sogar unmöglich, sich daran zu erinnern, woher sie kamen, aber es ist schade, sie wegzuwerfen
Sattelleder. Was ist das? Produkte daraus

Sattelleder. Was ist das? Produkte daraus. Grundlegende Eigenschaften, Eigenschaften und Merkmale von Sattelleder. Was ist eine Satteltasche. Sorten von Sattelleder: hart (yuft) und weich (roh). technisches Leder
Was ist ein Shuriken? Wie kann man es selbst machen?
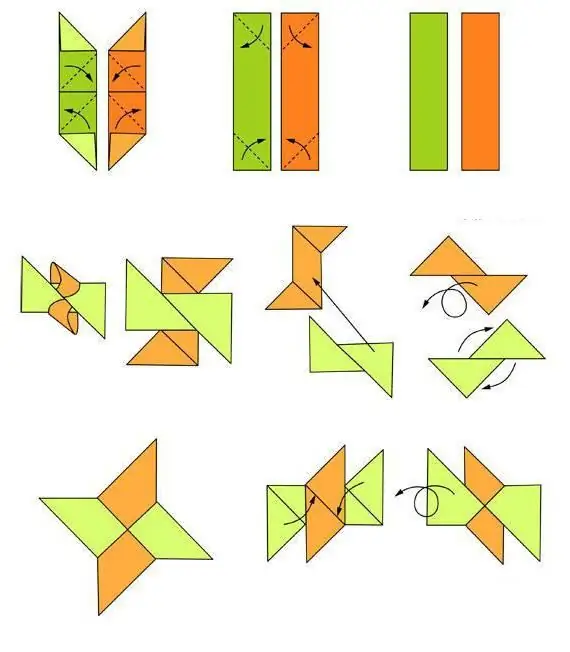
Natürlich wollte jeder Junge, nachdem er solche Filme gesehen hatte, seine eigene Shuriken haben. Niemand wusste, wie man es macht, also wurden Schallplatten, Blechstücke in Form von Sternen, manchmal sogar gewöhnliche Teller verwendet
Was kann man mit Bändern machen? Wie man Bandkugeln webt

Du weißt noch nicht, was man aus Bändern machen kann? Tanken Sie Geduld, Bänder und Fantasie. In diesem Artikel erklären wir Ihnen, welche Handarbeiten aus Satinbändern hergestellt werden können