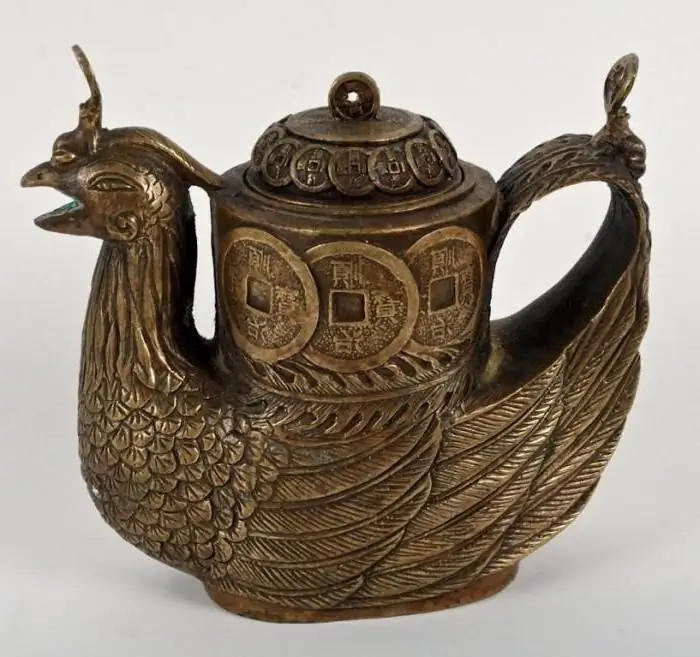
Inhaltsverzeichnis:
2025 Autor: Sierra Becker | [email protected]. Zuletzt bearbeitet: 2025-06-01 05:43
Um dem Interieur Assoziationen mit dem aristokratischen Stil des Mittel alters zu verleihen, verwenden Dekorationsmeister seit langem Messing und besonders oft Bronze. Das Gießen aus diesen Legierungen ermöglicht es schon heute, monumentale Meisterwerke zu schaffen, die jedes Zuhause schmücken können.
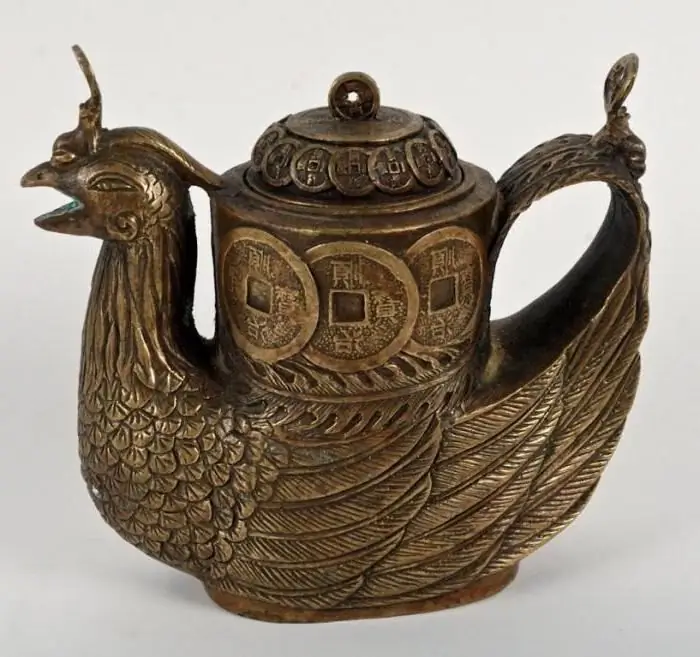
Bronze-Eigenschaften
Im Kunstguss werden Legierungen häufiger verwendet als reines Metall. Besonders beliebt ist Bronze - eine Legierung aus Kupfer mit Zinn (Zusatz- und Legierungselement) in verschiedenen Anteilen. Wird statt Zinn Zink zugesetzt, entsteht Messing, bei Zugabe von Nickel Kupfernickel. Auch Kupfer in Kombination mit Aluminium, Beryllium oder Silizium gilt als Bronze. Das Legierungselement ist in der Bezeichnung angegeben:
- BrO5, wobei Zinn 5 % beträgt;
- BrOS5-25: 5 % Zinn und 25 % Blei.
Was sind die technologischen Eigenschaften von Bronze? Gießen ist möglich, wenn das Material Fließfähigkeit erreicht. Die Temperatur, bei der Kupfer schmilzt, beträgt 1083 °C. Wenn Zinn hinzugefügt wird, sinkt die Schwelle auf 800 °C, was den Prozess des Erhitzens des Rohmaterials erheblich erleichtert. Nach dem Aushärten hat das Produkt einen Schrumpf von bis zu 1 %. Abhängig von den Komponenten unterscheiden sich Bronzeprodukte inHärte. Mit minimalem Zinnanteil lassen sie sich gut schmieden, ab einer Konzentration von 20 % werden sie hart und spröde. Plastizität wird durch die Einführung von Blei in die Zusammensetzung hinzugefügt. Der Zusatz von Zink macht das Material korrosionsbeständiger.
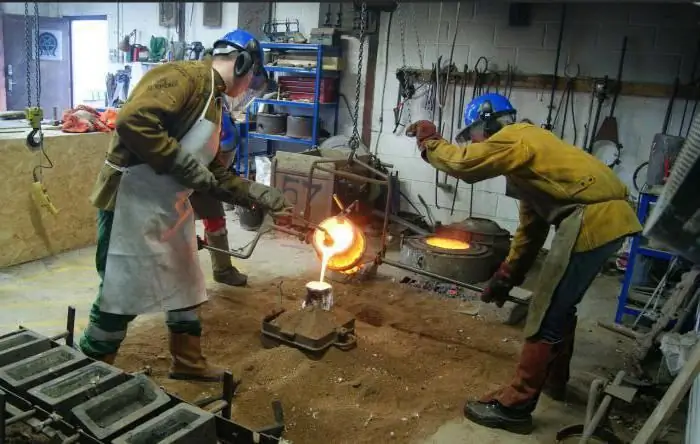
Bronze: Casting
Dem Schmelzen von Metallen gehen erhebliche Vorarbeiten voraus. Ein Teil davon bezieht sich auf die Herstellung des Modells. In dieser Phase formt der Bildhauer ein maßstabsgetreues Modell aus Kunststoff. Dann übersetzt er es lebensgroß in Gips oder Ton. Von diesem Übergangsmodell wird ein Rückenabdruck genommen. Eine komplexe Form hat mehrere konstituierende Elemente und wird in Teilen zusammengesetzt. Erhitztes Wachs wird hineingegossen. Wickeln Sie das Formular ein und erzielen Sie eine gleichmäßige Verteilung über die gesamte Oberfläche. Nach dem Abkühlen wird ein Modell der zukünftigen Skulptur aus Wachs geformt. Der Autor stellt die Details fertig, korrigiert die Mängel.
Der künstlerische Guss von Bronze und Messing wird überwiegend mit solchen Wachsausschmelzformen („Wachse“) durchgeführt. Die Skulptur ist hohl mit einer Wandstärke von 2-5 mm. Andernfalls, wenn das Metall die gesamte Form ausfüllen würde, wäre ein massiver Guss zu schwer und es wäre viel Material erforderlich. Und es sind nicht nur die Kosten. Beim Gießen wäre es notwendig, die gesamte Menge sofort zu schmelzen, und dies erhöht automatisch die Größe des Herds und des Ofens, verkompliziert den Vorgang des Zuführens der Legierung zur Form. Darüber hinaus führt das Schrumpfen des Materials zu einer unvermeidlichen Verformung, die zu einer Verzerrung der Formen und des Individuums führtZusammensetzungsdetails.
Prozessfunktionen
Nach dem Erstellen der Wachsform beginnt der nächste Schritt. Der Zauberer übernimmt. Er stellt seine eigene Form her, um geschmolzenes Metall zu gießen. Wachs wird in mehreren Schichten mit einer speziellen hitzebeständigen Zusammensetzung überzogen. Zunächst werden solche flüssigen Keramiken in die Wachsform gegossen. In diesem Stadium wird ein Kern erstellt - ein „Doodle“. Nachdem es mit der gleichen Zusammensetzung ausgehärtet ist, wird das Modell sorgfältig von außen bedeckt, wobei die erforderliche Anzahl von "Sommern" eingestellt wird, in die die Bronze geschickt wird.
Das Gießen wird nach dem Sintern (Kalzinieren) der Masse bei hoher Temperatur möglich. Als Ergebnis dieses Prozesses wird eine starke Keramikschale gebildet. Das Wachs wird durch die Lüftungs- und Luftauslässe verdunstet. Das Ergebnis ist eine Hohlform. Nach dem Gießen von Metall bricht es. Die innere Keramikschicht kann belassen oder auch durch das Zugangsloch entfernt werden.
![Kunstguss in Bronze und Messing [1] Kunstguss in Bronze und Messing [1]](https://i.designhomebox.com/images/025/image-72213-3-j.webp)
Bronzeguss zu Hause
Es ist auch möglich, einen Legierungsgegenstand in irdener Form zu erh alten. Wenn Sie zu Hause eine Schablone haben, können Sie auf diese Weise einen Bronzeguss anfertigen. Sie müssen sich jedoch darauf einstellen, dass es nicht möglich sein wird, kleine Details exakt zu kopieren, und es muss eine Verfeinerung vorgenommen werden. Die Form ist wegwerfbar, aber die Erde selbst (eine Mischung aus Ton und Sand) kann wiederholt verwendet werden. Machen Sie normalerweise abnehmbare Formen, die aus zwei Teilen bestehen. Sie können aber auch einteilig fertigen, wenn Sie ein Wachsmodell verwenden. Nach dem Sintern wird die Tonform eingekochtWasser schwimmt Wachs durch den Letnik an die Oberfläche.
Qualitätsguss kann erzielt werden, wenn die Form vorgeheizt wird. Kupfer und Zinn werden in einem Stahltiegel erhitzt. Verwenden Sie einen Kohleherd oder Muffelöfen. Nach dem vollständigen Schmelzen wird das Metall noch einige Minuten auf hoher Temperatur geh alten und in einem dünnen, kontinuierlichen Strahl in die Schmelze gegossen. Das Produkt wird nach dem Abkühlen zusätzlich verarbeitet. Zuerst wird das im Letniki eingefrorene Metall abgeschnitten. Plätze werden geräumt. Feine Details werden während des Prägeprozesses gebildet. Das Produkt wird geschliffen, poliert, ggf. mit Patina überzogen.
Empfohlen:
Wie erstelle ich eine dekorative Holzplatte an der Wand? Installationsanleitung

Die Dekoration eines Raumes mit dekorativen Brettern ist heute allgegenwärtig und passt zu fast jedem Stil. Auch wenn das Design Ihres Hauses oder Ihrer Wohnung im High-Tech-Stil geh alten ist, der sich durch das Vorhandensein von Schwarz und Weiß auszeichnet, können Sie problemlos Holzverkleidungen darin anbringen, die es wärmer machen
DIY dekorative Kerzen

Was gibt es Schöneres als selbstgemachte Kerzen? Wir analysieren alle Phasen dieses Prozesses und umgehen die Fallstricke
Anwendungsarten. Dekorative Anwendung: Meisterklasse
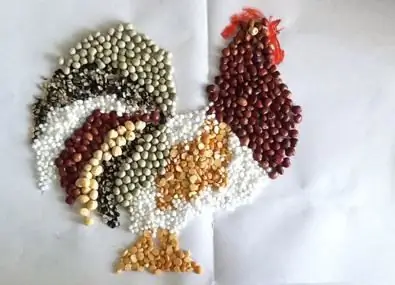
In der Übersetzung aus dem Lateinischen bedeutet das Wort "Anwendung" "Anhaftung". Um ein Bild mit dieser Technik zu erstellen, müssen Sie verschiedene Formen aus demselben Material ausschneiden und auf der Basis, dem Hintergrund, befestigen. Für die Arbeit können Sie Papier, Stoff, Müsli und viele andere improvisierte Mittel verwenden. Lassen Sie uns einen genaueren Blick darauf werfen, welche Arten von Anwendungen es gibt und welche Merkmale ihre Erstellung haben
Häkelkissen: Diagramm und Beschreibung. Dekorative Kissen häkeln

Näherinnen stellen gehäkelte Kissen in ganz unterschiedlichen Formen her. Sie sind quadratisch, rund, zylindrisch. Ihre Größe reicht von winzig bis riesig
Dekorative Verzierung - was ist das?

Die Geschichte der Ornamente und dekorativen Motive begann in der Antike. Genauer gesagt während der Altsteinzeit. Was ist ein dekoratives Ornament? Dies ist ein Bild, das nicht nur ästhetischen Genuss bietet, sondern auch eine gewisse Wirkung auf eine Person hat. Eine solche Zeichnung weckt eine Reihe von Assoziationen, die es Ihnen ermöglichen, die Arbeit zu bewerten und zu verstehen