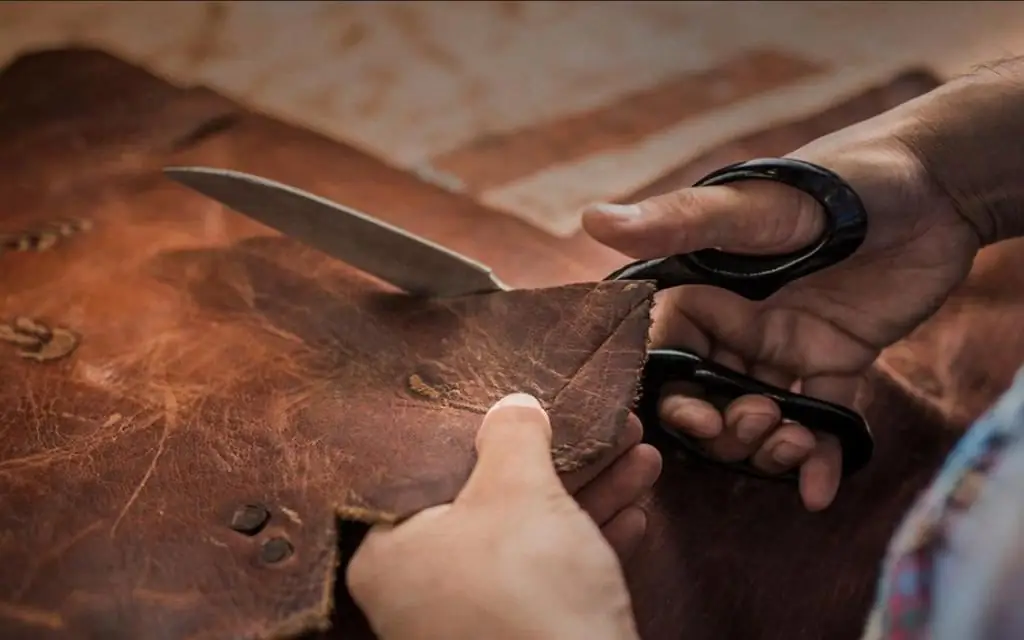
Inhaltsverzeichnis:
2025 Autor: Sierra Becker | [email protected]. Zuletzt bearbeitet: 2025-06-01 05:43
Leder ist ein natürliches, umweltfreundliches Material, das sich flexibel verarbeiten lässt. Es ist weich, fühlt sich angenehm an und ist langlebig. Wenn Sie damit arbeiten, können Sie Ihre Kreativität zeigen und einzigartige Produkte aus unnötigen, alten Dingen herstellen. In dem Artikel werden wir betrachten, was künstlerische Lederverarbeitung ist.
Materialarten

Folgende Sorten existieren:
- Echtes Leder wird durch Verarbeitung der Haut eines Tieres hergestellt, es hat eine faserige Struktur.
- Kunstleder wird industriell aus Polymermaterial hergestellt.
- Velours ist eine Chromledervariante mit Schäden an der Außenseite. Dadurch wird es auf der falschen Seite unter Wildleder gesteckt.
- Laika ist ein Leder mit einer charakteristischen Duktilität und Weichheit. Es wird aus den Häuten kleiner Rinder, Schafe und Ziegen hergestellt.
- Wildleder - Leder aus der Haut von Elchen, Hirschen oder Wildziegen mit Fettgerbung. Verfügt über eine samtigeOberfläche und Weichheit, auf der Vorderseite hat einen kurzen, samtigen Flor.
- Opoek - hochelastisches weiches Leder. Hergestellt aus den Häuten neugeborener Kälber.
- Wachstum ist die Haut eines jungen Tieres. Allerdings ist es nicht so elastisch wie das Kalb, da sich das Tier nicht mehr von Milch, sondern von pflanzlichen Lebensmitteln ernährt.
- Saffiano - aus leicht angebrannter Ziegenhaut. Es ist sehr weich und dünn und in verschiedenen Farben erhältlich.
- Chevret - dichte und gleichzeitig elastische Haut. Hergestellt durch Chromgerbung aus Schaffellen. Seine Dicke reicht von 0,6 bis 1,2 mm.
- Chevro ist ein dichtes und weiches Leder aus Ziegenhäuten mit Chromgerbung. Es hat ein ungewöhnliches Muster und eine Dicke von 0,4 bis 1 mm.
- Reptilienhaut - einzigartiges Muster, hohe Qualität und hohe Kosten.
Was ist Lederkunst?
Dies ist ein Material, das als eines der ersten von Menschen fertiggestellt wurde. Natürlich wurde es ursprünglich für häusliche Zwecke verwendet. Später erschienen dekorative Dekorationstechniken wie Gravuren und Applikationen. Auch nach der Entdeckung des Webens ist Leder immer noch das Hauptmaterial für die Herstellung von Gürteln, Taschen, Rüstungen und Schuhen.
Es gibt drei Hauptstadien des Anziehens. Nach der Vorarbeit - Häuten und Reinigen - wird aus dem Fell ein ungegerbtes Halbzeug, eine sogenannte Haut. Es hat besondere Eigenschaften, je nachdem aus welchem Leder eine bestimmte Art hergestellt wird. Anschließend wird die Struktur des Rohmaterials durch Gerben fixiert. Finishing-Verfahren werden durchgeführt, um zu gebennackte physikalische, technologische und andere Eigenschaften sowie das gewünschte Aussehen.
Die Technologie der Lederverarbeitung in verschiedenen Nationalitäten hat ihre eigenen Merkmale. Der Hauptzweck der Gerbung bestand darin, die Haut vor Fäulnis und Fäulnis zu schützen. Die älteste Verarbeitungsart ist die Aldehydgerbung. Es besteht darin, die Haut im Rauch von brennenden Pflanzen zu h alten. Die Nomaden bestrichen es mit tierischem Fett, und die Indianer rieben eine Mischung aus Fett und Eiern ein. Danach wurde das Material mit Wasser gewaschen und mit abgerundeten Steinen geknetet. Es war eine Methode der Fettgerbung.
In den nördlichen Völkern und in Indien wurde dieser Prozess mit Hilfe von Kräuter- und Gemüsesud durchgeführt. Diese Methode wird vegetabile Gerbung genannt. In asiatischen Ländern wurde ein anderer Typ verwendet. Die Gerbung mit Alaun erfolgte durch Mischen von Mehl, Salz, Eigelb und Aluminiumalaun, und dann wurde das Leder mit der resultierenden Zusammensetzung behandelt.
Interessante Fakten
Die Geschichte der kunstvollen Lederverarbeitung reicht bis in die Antike zurück.
Die Naturvölker nutzten Tierhäute, um sich vor schlechtem Wetter zu schützen. Unter dem Einfluss von Feuchtigkeit und Temperaturen hielten sie jedoch nicht lange. Daher sind bis heute nur wenige Gegenstände aus diesem Material erh alten. Im Laufe der Zeit beginnen die Menschen, die Haut zu verarbeiten und ihre Lebensdauer zu verlängern. Bei Ausgrabungen ägyptischer Gräber wurden Felsmalereien aus dem 5. Jahrhundert v. Chr. entdeckt. h., die den Abrichtvorgang demonstriert.
Handwerker dieser Zeit beginnen Geschirr, Säcke, Schuhe, Kleider aus Leder herzustellen. Die über den Rahmen gespannten Felle dienten als Navigationsmittel. Nomaden bauten nach einem ähnlichen Prinzip Behausungen, und für Krieger wurden Schilde aus Leder gefertigt. Später beginnen Handwerker, ihre Fähigkeiten zu verbessern und kreativ an die Verarbeitung des Materials heranzugehen. Im Grab von Tutanchamun wurden mit Gold bestickte Kleidungsstücke, mit Lederapplikationen verzierte Haush altsgegenstände usw. gefunden.
Römer im 1. Jahrhundert v e. begannen, solche Methoden zur Verarbeitung der Haut anzuwenden, die es ermöglichten, sie als Pergament zu verwenden. Sie befestigten die Laken und schufen so den Anschein eines Buches. Später entwickelte sich die Buchbinderei. Seit dem 10. Jahrhundert werden Einbände mit kunstvollen Prägungen, Stempeln und Gravuren kunstvoll verziert. Der gesamte Einband war mit Ornamenten bedeckt. Es zeigte die einfachsten geometrischen Formen, Tiere, Pflanzen und mehr.
Mit dem Aufblühen des gotischen Stils verbreitete sich die Gravurtechnik. Es unterschied sich in der Komplexität und wurde nur von qualifizierten Handwerkern durchgeführt. Bis heute gelten die erh altenen Produkte der Gotik als Meisterwerke der Kunst und werden in den besten Museen der Welt aufbewahrt.
In der Renaissance wird eine solche Technik der kunstvollen Lederverarbeitung (Foto ist im Artikel zu sehen) als exquisite Prägung populär. Reliefbilder mythologischer Figuren werden auf Objekten reproduziert. Der Barockstil bringt Tapeten aus Leder in Mode. Zuerst wurden sie in Nordafrika, später in Spanien hergestellt und im 17. Jahrhundert in Europa weit verbreitet. Mit dem Aufkommen des Klassizismus traten jedoch im 19. Jahrhundert keine neuen Trends in der Lederveredelung auf, vor dem Hintergrund der Popularität der Moderne, Gravuren, Intarsien undVergoldung.
Bei Ausgrabungen im Altai wurden auch Lederartikel aus dem 5.-1. Jahrhundert v. Chr. gefunden. B. Geschirr, Gefäße, Kisten. Die Gerbereiindustrie unter den Slawen war ziemlich gut entwickelt, aber eine kleine Anzahl von Dingen hat bis heute überlebt. Hauptsächlich Schuhe und andere Haush altsgegenstände.
Was ist das Ziel
Lederbearbeitungswerkzeuge sind nichts Besonderes. Die meisten von ihnen sind weit verbreitete Haush altsgegenstände.
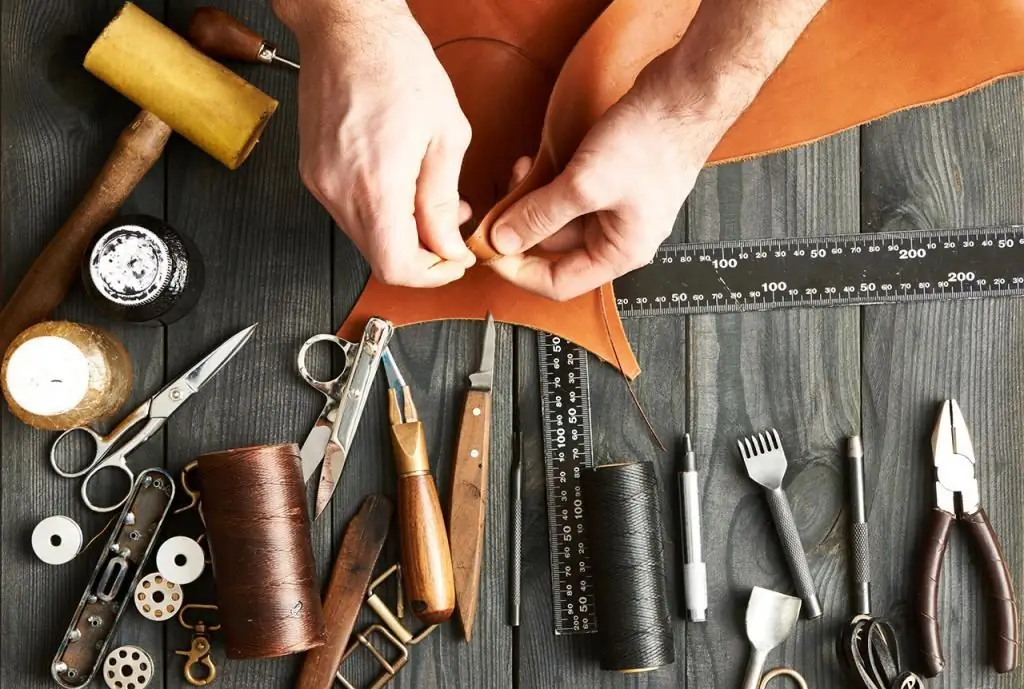
Die Zubehörliste lautet wie folgt:
- Cuttermesser für die Bearbeitung dicker Leder.
- Stanzmesser.
- Graviermesser schmal.
- Schneiderschere.
- Holzplatte oder Glas zum Schneiden von Leder.
- Schere mit Zickzack-Klinge.
- Rundlocher, benötigt zum Stanzen von Löchern für Beschläge oder Flechtwerk.
- Nagelschere.
- Lochstanzen mit einem Durchmesser von 30-40 mm zur Herstellung von Knöpfen, Lederohrringen und anderen Arten von Accessoires und Schmuck.
- Briefmarken. Sie sind ein Stab, an dessen Ende das einfachste Reliefmuster geschnitzt ist. Wird für die Oberflächendekoration verwendet.
- Schlitzstempel. Sie dienen zum Stanzen von rechteckigen Löchern, in die bei der Perforationstechnik Bänder eingefädelt werden.
- Lockenlocher zum Perforieren verschiedener Formen in Form eines Sterns, Herzens usw.
Lederverarbeitungsschritte
Die Arbeit an einem beliebigen Produkt erfolgt in drei Schritten. Sequenzierungist:
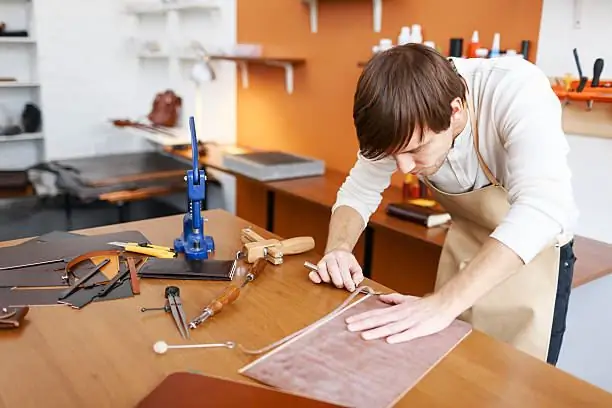
- Planung von Form, Farbe, Bearbeitung und Verbindung von Elementen.
- Erstelle ein Muster. Die Haut wird nach dem Muster geschnitten. Bei Bedarf bereiten sie auch Dekorationselemente vor.
- Verbindungsteile.
- Fertigstellung des Produkts.
Betrachten Sie als Nächstes die Techniken und Merkmale der Verarbeitung von Produkten aus echtem Leder.
Bräunen
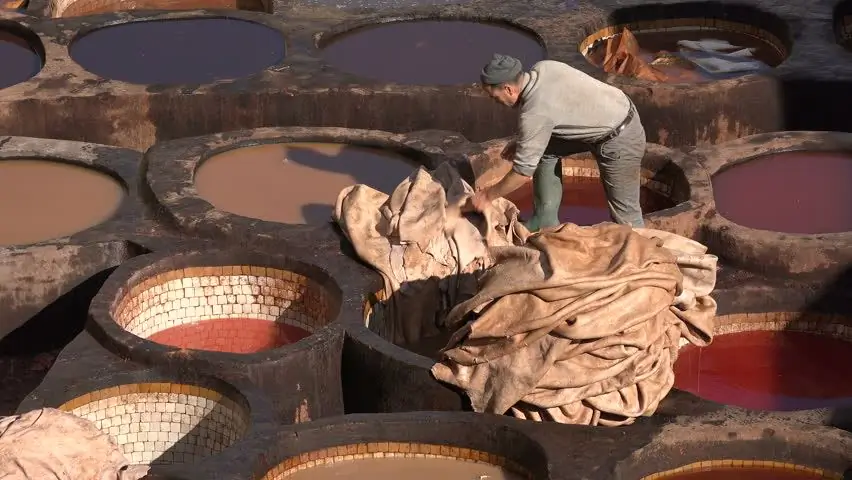
Dies ist eine Lederverarbeitungstechnik, bei der verschiedene Substanzen verwendet werden, um dem Material Festigkeit, Elastizität und verbesserte Leistung zu verleihen. Vor dem Gerben werden die Häute mit einer konzentrierten Salzlösung eingerieben, die mehrere Tage in Wasser und Kalkmörtel eingeweicht wird. Dann wird die auf der Haut verbliebene Muskelfett- und Haarschicht entfernt. Das Material wird dann auf die gleiche Weise für eine bessere Duktilität und Festigkeit nachbehandelt.
Prägung
Es gibt verschiedene Arten dieser Verarbeitung. Unter industriellen Bedingungen werden mehrere Prägeverfahren verwendet, indem ein Muster unter Verwendung von Formen extrudiert wird. Bei der Herstellung von Dekorationsprodukten wird es mit speziellen Satzstempeln und Stempeln durchgeführt.
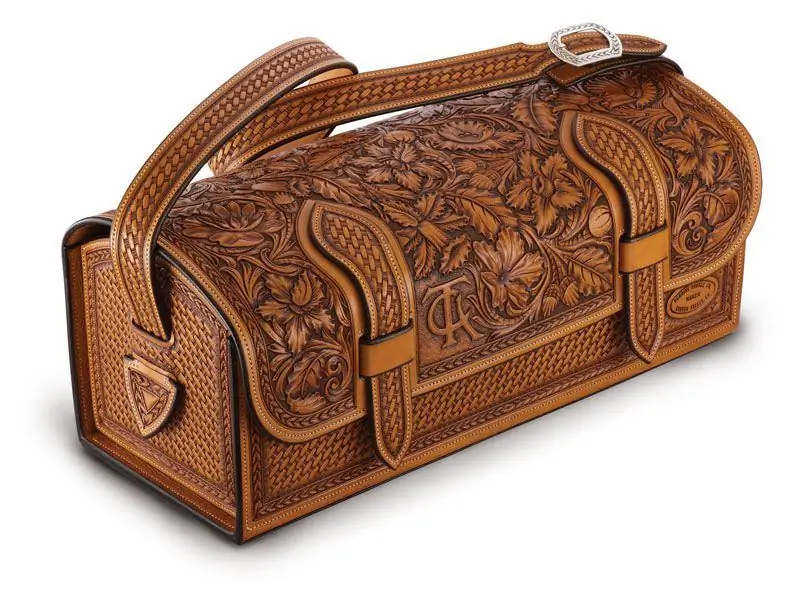
Eine andere Art der künstlerischen Verarbeitung von Leder (das Foto ist im Artikel dargestellt) - Prägen mit Füllung - wird wie folgt durchgeführt. Reliefelemente werden aus einer dichten Unterlage ausgeschnitten und unter das angefeuchtete Material gelegt. Dann wird es entlang der Kontur geprägt. Kleine Elemente werden ohne Futter herausgedrückt, das Relief wird erreichtHautdicke zählen. Während es trocknet, härtet es aus und behält sein Relief.
Thermisches Prägen erfolgt durch Extrudieren von Teilen mit erhitzten Metallstempeln.
Stanzen und Weben
Dies ist eine der ältesten Lederkunsttechniken.
Perforation besteht darin, Löcher mit unterschiedlich geformten Stempeln in Form eines Musters zu schneiden. Diese Technik wird verwendet, um durchbrochene Kompositionen auszuführen, z. B. Schmuck, Tafeln oder das Verzieren von Kleidung.
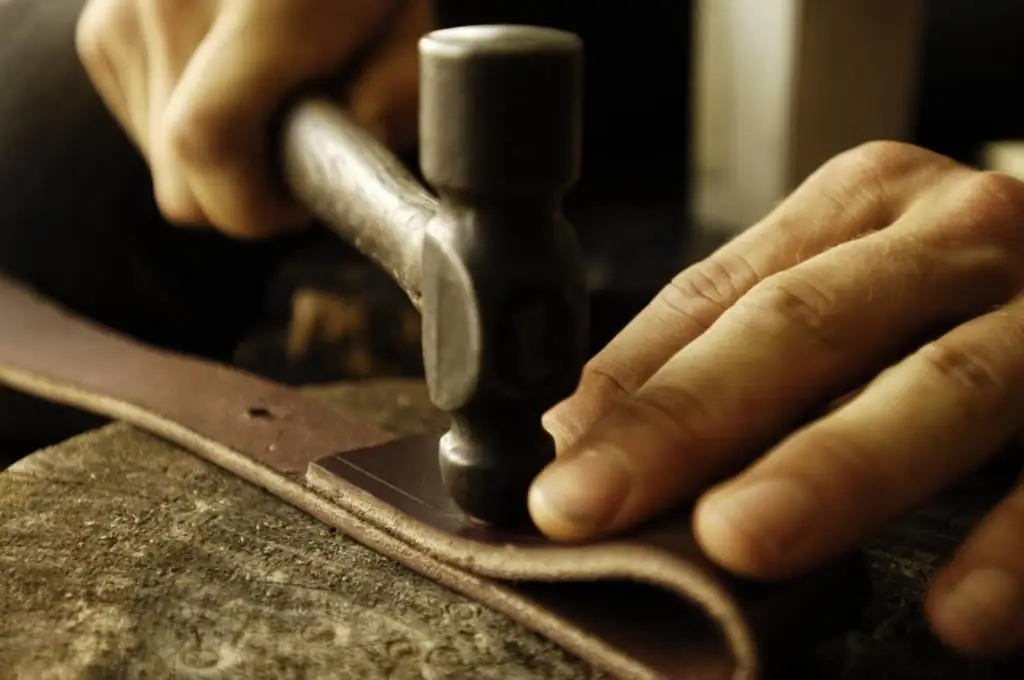
Das Weben von Lederschnüren findet sich häufig bei der Herstellung von Armbändern, Gürteln und Schnürsenkeln. Taschen, Kleider und Schuhe werden so fertig.
Brandmalerei
Diese Technik ist bekannter als Ausbrennen. In der traditionellen Version besteht die Brandmalerei darin, verschiedene Muster auf die Oberfläche dichter Lederarten aufzubringen. Dies geschah mit Kupferstempeln, die auf eine bestimmte Temperatur erhitzt wurden.
Das fertige Bild hängt direkt von den Fähigkeiten des Künstlers ab, daher ist es von großer Bedeutung, zu lernen, wie man Leder in dieser Technik verarbeitet. Auch die Fähigkeiten des Brenngeräts spielen eine große Rolle. Mit dem Pyrographen können Sie dünne und sehr komplexe Muster auf das Produkt aufbringen. Oft wird dieser Look mit anderen Techniken kombiniert: Gravieren, Prägen und Malen.
Gravur und Applikation
Diese Art der kunstvollen Lederverarbeitung wird nur auf dichten Stoffarten wie Satteldecke, Yuft, Shora durchgeführt.
Die Gravur erfolgt wie folgt. Auf die Vorderseite der benetzten Haut wird mit einem Cutter ein Muster aufgebracht. Danach MetallDas Objekt erweitert die Schlitze und füllt sich mit Farbe. Ein anderes Gravierverfahren beinh altet die Verwendung eines Pyrographen. Das endgültige Muster, seine Farbe und Dicke hängen hauptsächlich vom Glühgrad der Nadel des Geräts ab.
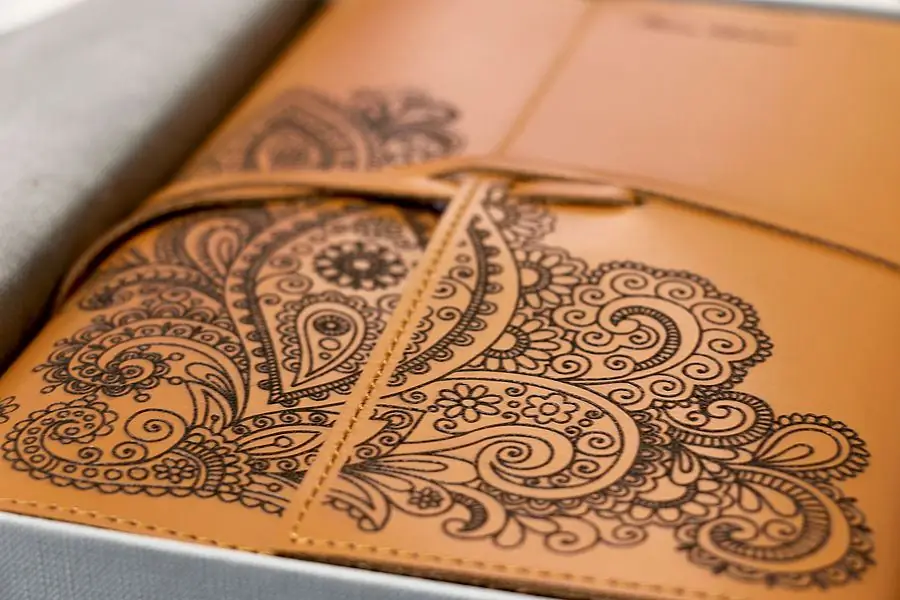
Applikationen auf Kleidung werden durch Aufnähen von dekorativen Elementen aus dünnem Leder auf die Basis hergestellt. Um Souvenirs, Paneele und andere Einrichtungsgegenstände herzustellen, können Teile aus allen Arten von Materialien hergestellt und auf die Basis geklebt werden.
Intarsien
Diese Technik ist eine der ältesten aller aufgeführten. Es ist eher wie ein Mosaik oder Inlay. Die Haut wird gefärbt und Details werden gemäß den Mustern ausgeschnitten. Dann werden sie mit Knochenleim oder PVA auf eine Textil- oder Holzunterlage geklebt. Intarsien werden verwendet, um Paneele, Schmuck, Souvenirs und Möbel zu dekorieren.
Batik, Tonen, Kerzenverarbeitung, Rösten
Schauen wir uns einige weitere interessante Möglichkeiten zum Abschluss an:
- Die Technik, bei der das Ornament mit geschmolzenem Paraffin auf die Oberfläche von Naturleder aufgetragen wird, nennt man Batik. Nach dem Beschichten wird eine Farbzeichnung angefertigt, während die Stellen mit Wachs ihr unberührtes Aussehen beh alten. Nach dem Lackieren wird das Wachs mit einem stumpfen Gegenstand entfernt.
- Das Abtönen erfolgt mit einem Brenner. Zuerst wird eine Skizze auf die Haut aufgetragen und dann werden mit einer Nadel Ornamentlinien gezogen. Je nach Erwärmung der Nadel und Druckkraft bleibt ein Bild unterschiedlicher Farbtöne auf der Unterlage.
- Eine recht einfache und ungewöhnliche Methode ist es, das Material auf einer Kerze zu verarbeiten. Elemente werden gemäß der Vorlage geschnittenHaut. Auf der Vorderseite werden mit einem spitzen Gegenstand kleine Einschnitte gemacht und über der Flamme einer Kerze leicht angesengt. Diese Methode eignet sich am besten zur Simulation der Adern auf den Blättern von Pflanzen und Blütenblättern. Auf diese Weise lassen sich Schnüre bequem zum Flechten verarbeiten.
- Rösten ist eine weitere thermische Art der Lederverarbeitung. Die linke Seite des Materials wird in eine heiße Bratpfanne mit der gewünschten Temperatur gelegt. Bald bildet sich auf der Oberfläche ein Kreis, der dem Produkt eine konvexe Form verleiht. Das Rösten wird am häufigsten verwendet, um sperrige Teile herzustellen.
Vorhänge
Diese Methode ist die einfachste und schönste Art, Leder zu behandeln. Für diese Technik werden in der Regel weiche Materialarten gewählt. Die Haut wird reichlich mit Klebstoff bestrichen und an der Basis befestigt. Ohne auf das Trocknen zu warten, werden F alten gemäß der Skizze in die richtige Richtung gebildet. Wenn der Vorhang aus gebrauchtem Leder besteht, wird es vorgereinigt und bei Bedarf gefärbt.
Empfohlen:
Vignettierung - was ist das in der Fotografie? künstlerische Fotografie
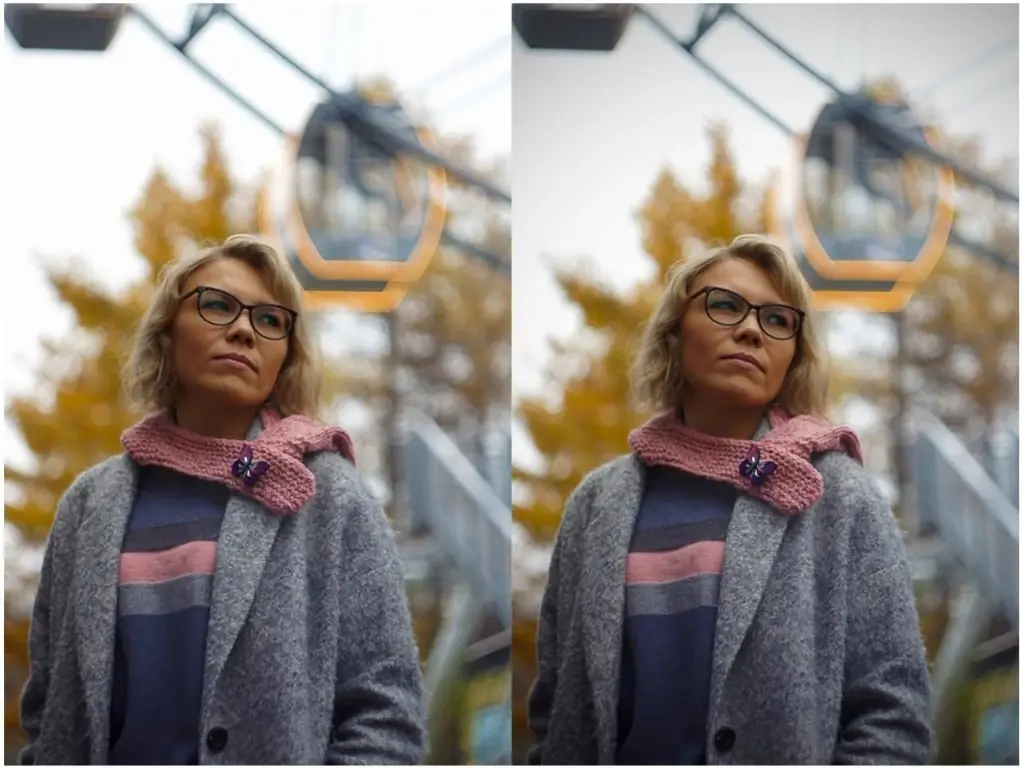
Es gibt unzählige Möglichkeiten, das Wichtigste im Rahmen hervorzuheben. Dazu können Sie verschiedene Licht- und Farbmethoden verwenden oder sich auf Linien und Rahmen konzentrieren. Aber der einfachste und schnellste Weg zur Auswahl ist die Vignettierung. Was ist das? In unserem Artikel werden wir diese Frage ausführlich beantworten
Abramtsevo-Kudrinskaya Holzschnitzerei: Geschichte, Technik, Besonderheiten

In dem Artikel werden wir die Geschichte und Technologie der Abramtsevo-Kudrinskaya-Schnitzerei betrachten, die die Produktion und den zukünftigen Fischfang organisierte. Machen wir den Leser mit den Merkmalen des Arbeitsstils vertraut, bei dem Flachrelief und geometrisches Schnitzen erfolgreich kombiniert werden. Rhythmische Blumenornamente sind auf Haush altsgegenständen dieser Zeit zu sehen. Das sind Schöpfkellen und Salzstreuer, dekorative Kästen und Vasen, große Teller und Schalen
Ist Verzerrung ein Imagefehler oder eine ungewöhnliche künstlerische Entscheidung?
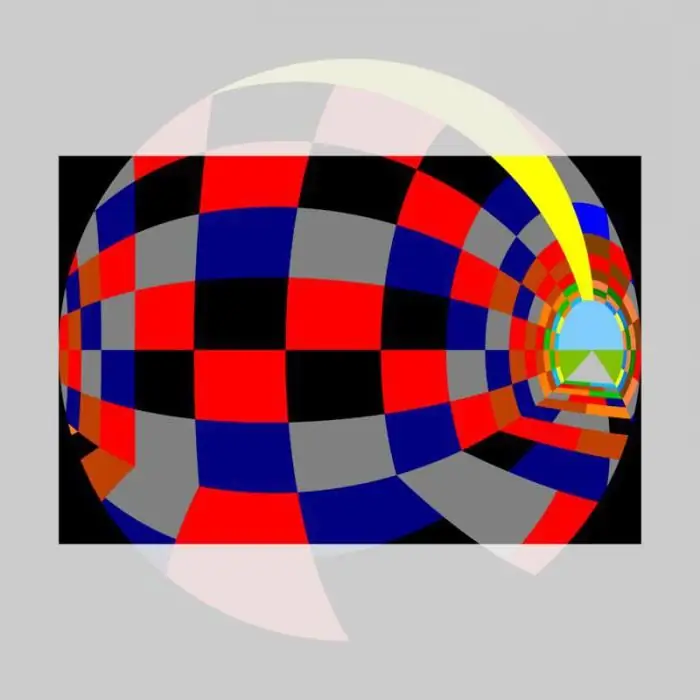
Dieser Artikel widmet sich einem Phänomen wie Verzerrung, Methoden zur Beseitigung dieser Verzerrung aus einem Bild während der Aufnahme oder beim Bearbeiten eines Bildes sowie absichtlicher Verzerrung
Künstlerische Bearbeitung von Fotos in Photoshop
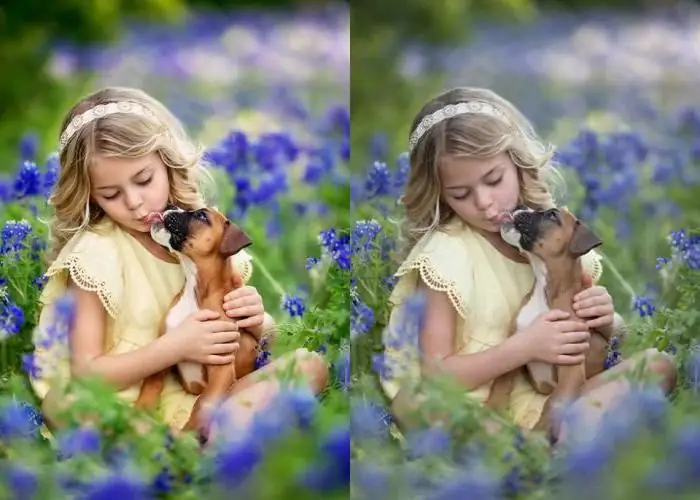
Im Zeit alter der modernen Technologie werden auch Kameras den Anforderungen gerecht. Eine Fülle von Objektiven für unterschiedliche Aufnahmegenres, Filter und Spezialobjektive helfen dabei, fast auf Anhieb eine tolle Aufnahme zu machen. Aber auch hier gibt es diejenigen, die noch besser werden wollen. Dank dessen sind verschiedene Programme zur künstlerischen Fotobearbeitung sehr beliebt. Sogar ein Kind kennt den Namen der häufigsten von ihnen. Die Rede ist natürlich von Photoshop
Was ist Whist: Herkunft, Regeln, Besonderheiten bevorzugt

Der Name des Spiels leitet sich vom englischen Whist ab – „sei still“, „still“, „ruhig“. Denn das Spiel erfordert wirklich Konzentration, Aufmerksamkeit und Ruhe. Es geht vor allem darum, im Spiel gegen den bestochenen Partner die maximalen Stiche zu sammeln, für die entsprechende Punkte vergeben werden