
Inhaltsverzeichnis:
2025 Autor: Sierra Becker | [email protected]. Zuletzt bearbeitet: 2025-01-22 22:11
In den 30er Jahren des letzten Jahrhunderts wurde ein so wunderbares Material zum Basteln wie Fimo erfunden. Zuerst wurden Teile von Puppen daraus hergestellt, aber die Plastizität, die einfache Arbeit mit dem Material und die H altbarkeit der Produkte eroberten schnell die Herzen der Handwerker, und Ton wurde zur Herstellung von Souvenirfiguren und Schmuck verwendet. Polymer Clay ist besonders beliebt bei der Herstellung von Blumenarrangements. Keramikfloristik ist zu einer eigenständigen Kunstform geworden, und mit dieser Technik hergestellte Innenblumen können in Schönheit mit lebenden Pflanzen konkurrieren. Raffinesse und Langlebigkeit haben sie zu einem wesentlichen Merkmal von Hochzeitsfeiern gemacht. Schließlich verwelkt ein Plastikstrauß nicht und erfreut viele Jahre lang mit Schönheit, die an den Geburtstag der Familie erinnert.
In diesem Artikel erfahren Sie, wie Sie mit Ihren eigenen Händen Pfingstrosen aus Fimo herstellen und welche Art von Ton für Innenblumen und Schmuck geeignet istund welche Werkzeuge für den Job benötigt werden. Fangen wir also an.
Tonarten
Polymerton ist ein Material für dekorative Kunst, aus dem Puppen, Schmuck, kleine Skulpturen und Innenblumen hergestellt werden. Es gibt 2 Arten der plastischen Chirurgie:
- selbsthärtend;
- Thermoplast.
Die erste Art von Material ist, abhängig von den zugrunde liegenden Komponenten, "schwer" und "leicht". Aus „schwerem“Kunststoff werden Puppen und deren Einzelteile hergestellt. In seiner Struktur ähnelt es natürlichem Ton. Produkte aus dem Material sind rau, sie können geschliffen, mit Öl- und Acrylfarben bem alt, lackiert werden. Der Nachteil von Keramoplast ist eine hohe Schrumpfung der Produkte nach dem Trocknen und die Wahrscheinlichkeit von Rissen.
Bei der Herstellung von Puppen verwenden professionelle Handwerker einen speziellen "Puppen" -Ton, mit dem Sie das Produkt auch nach dem Trocknen anpassen können: Schleifen, Überschuss abschneiden. Ton kann bei Bedarf sogar eingeweicht werden, um die Zusammensetzung zu ändern. Sein Hauptvorteil ist weniger Schrumpfung.
„Leichte“Kunststoffe werden für Blumenarrangements verwendet. Der beliebteste in Japan hergestellte Ton auf Zellulosebasis. Dies ist ein sehr weiches und plastisches Material, mit dem Sie dünne durchscheinende Blütenblätter herstellen können, die optisch kaum von natürlichen zu unterscheiden sind. Fertige Blumen sind matt und ähneln Papier. Solche Produkte vertragen keine Feuchtigkeit. Ein Blumenstrauß aus Fimo-Pfingstrosen wird Ihr Wohn- oder Schlafzimmer schmücken und niemals verwelken.
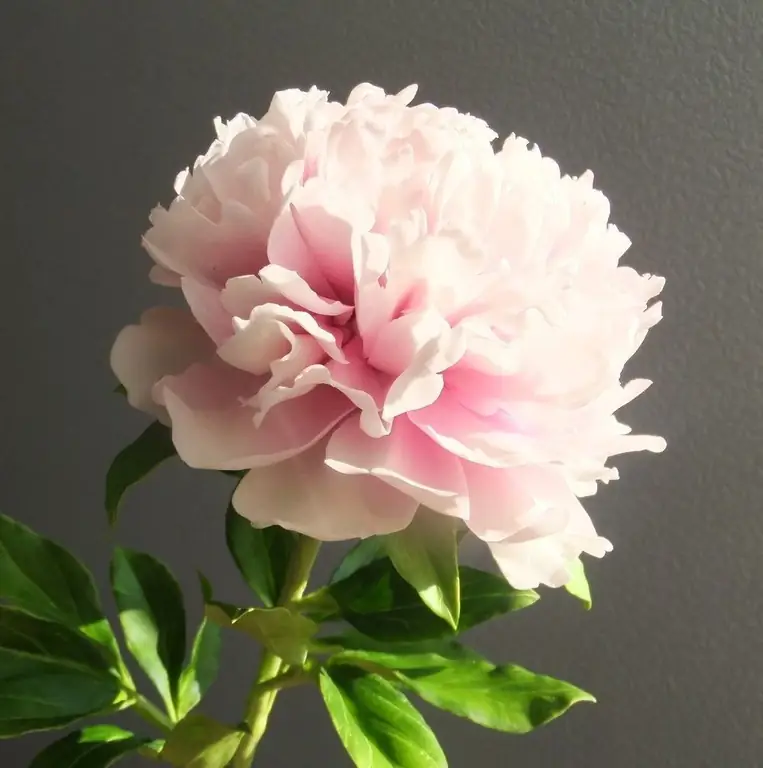
Der Ursprung der Keramikfloristik als Kunst ist mit dem Auftreten von "k altem Porzellan" verbunden. Es basiert auf einer Mischung aus PVA-Kleber und Maisstärke. Im Verkauf ist das am häufigsten verwendete Material weiß, getönt mit Ölfarbe. Fertige Produkte können mit Acryl bem alt werden. Blumen aus "k altem Porzellan" sind flexibel und realistisch, sie haben keine Angst vor Feuchtigkeit. Meister empfehlen die Herstellung von Fimo-Pfingstrosen aus dieser Art von Kunststoff. Die besonderen Eigenschaften des Materials ermöglichen die Herstellung von exquisitem Modeschmuck, verziert mit winzigen, fast „lebendigen“Blumenarrangements. Auf den Fotos im Artikel sehen Fimo-Pfingstrosen so realistisch aus, dass es schwierig ist, sie von echten zu unterscheiden!
Die zweite Art von Fimo, Thermoplast, wird auf der Basis von Polyvinylchlorid und Weichmachern hergestellt, die beim Erhitzen verdampfen. Die Produkte werden bei einer Temperatur von 110-130 Grad Celsius in einem Ofen gebacken oder gekocht. Thermoplastische Produkte sind stark und widerstandsfähig. Dieser Ton eignet sich hervorragend für die Herstellung von Schmuck. Wenn Sie sich also entscheiden, eine Pfingstrosenbrosche aus Polymerton herzustellen, wählen Sie sie aus. Das Material ist flüssig (in Form eines Gels), gewöhnlich (es ähnelt in seiner Struktur Wachsplastilin), durchscheinend und mit Füllstoffen (Metallpulver, Glitzer usw.).
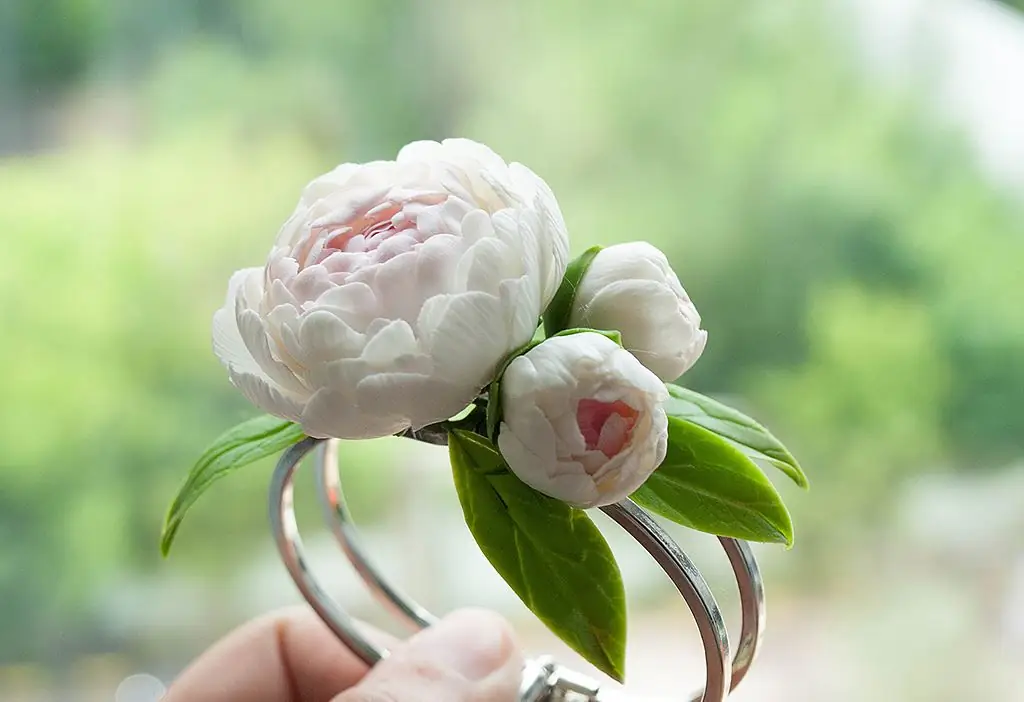
Werkzeuge und Materialien
Bevor Sie beginnen, eine Fimo-Pfingstrose in voller Größe zu erstellen, müssen Sie Materialien und Werkzeuge für die Arbeit vorbereiten.
- "K altes Porzellan". Anfängerinnen wird empfohlen, Kunststoff auf Zellulosebasis zu verwenden, „k altes Porzellan“ergibt jedoch h altbarere Produkte und kann im „rohen“Zustand mit Ölfarben getönt werden.
- Latexkleber. Nützlich zum Verbinden von Teilen.
- Verdünner und Ölfarben. Weiß, rot, grün.
- Schimmel. Dies sind spezielle Rohlinge, die die Textur der Blütenblätter und Blätter natürlicher Blumen imitieren. Sie bestehen aus Acryl, Silikon, Epoxid und anderen geeigneten Materialien. Formen können in Fachgeschäften gekauft oder selbst hergestellt werden. Wenn die Pfingstrosentexturen nicht zur Hand waren, können Sie eine Rosenform für die Blütenblätter und Hortensien für die Blätter verwenden.
- Dicker und dünner Draht. Der erste ist für den Stamm, der zweite für die Blätter.
- Rundzange.
- Nudelholz aus Ton, Stapel in verschiedenen Größen, Stapel mit Kugelenden, Rollerblade, Nagelschere.
- Klebeband. Wird benötigt, um die Blätter am Stängel zu befestigen.
- Pinsel für Kleber und Farben.
Anfängerinnen interessieren sich oft für die Frage, wie man eine Pfingstrose aus Fimo formt. Daran ist nichts Schwieriges, die Hauptsache ist, sich mit Geduld, Zeit und hochwertigen Materialien für die Arbeit einzudecken.
Blätter
Also fangen wir damit an, Pfingstrosenblätter aus Fimo herzustellen.
Schneiden Sie einen dünnen Draht in 7-8 cm lange Stücke, Sie benötigen 6 Sockel.
Jetzt musst du den Ton kneten. Wir kneten ein Stück Plastik und fügen ein wenig grüne Ölfarbe in die Mitte, vorsichtig, um es nicht zu tunverschmutzen, kneten Sie das Material, bis eine einheitliche Farbe erreicht ist. Als nächstes rollen Sie die Schicht mit einer Dicke von etwa 2 mm aus. Mit einem Rollenschneider 2 Kleeblätter und 4 Blätter ausschneiden. Rohlinge können mit einer Schere beschnitten werden. Wir rollen die Ränder der Blätter mit einem Stapel mit einer Kugel, um sie dünner und realistischer zu machen. Als nächstes benötigen Sie eine Form. Wir übertragen die Textur der Adern, drücken die Plastikrohlinge vorsichtig auf die Form, biegen die Blätter entlang der zentralen Ader und legen den mit Klebstoff bestrichenen Draht hinein. Trocknen lassen.
Blütenblätter
Lassen Sie uns zuerst den Kern der Pfingstrose aus Fimo machen.
Mit einer Rundzange eine Schlaufe am Ende des dicken Drahtes machen. Dies ist der zukünftige Stamm. Wir rollen eine Kugel mit einem Durchmesser von etwa 1 cm aus grünem Plastik und geben ihr eine Tropfenform. Wir schneiden die schmale Spitze des Werkstücks mit einer Schere in 5 Teile. Versuchen Sie, sie ungefähr gleich zu h alten. Wir begradigen die Enden in verschiedene Richtungen. Habe ein Sternchen. Schmieren Sie die Schlaufe am Draht mit Klebstoff und „legen“Sie den Kern der zukünftigen Pfingstrose darauf. Wir entfernen überschüssigen Klebstoff, nivellieren den Kunststoff und glätten die Fugen. Mit einem Rollenmesser schieben wir fünf Aussparungen entlang des Kerns und simulieren das Relief der Venen. Werkstück trocknen lassen.
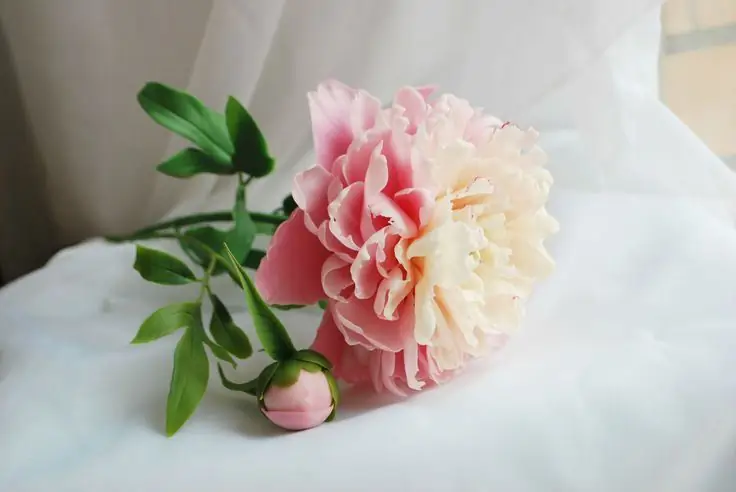
Um Pfingstrosenblätter aus Fimo herzustellen, brauchst du ein großes Stück Plastik. Wir tönen es mit roter Ölfarbe. Die Pfingstrose hat drei Arten von Blütenblättern: kleine schmale, mittlere und runde große. Um den ersten Typ herzustellen, benötigen Sie ein Stück Ton mit einem Durchmesser von 1 cm, das wir Ihnen gebendie Form eines Tropfens in der Höhe des Blütenblattes. Wir rollen das Werkstück in einem Stapel aus und erzeugen die gewünschte Form. Wir reißen die Kante leicht ein, damit das Werkstück einem echten Blütenblatt so ähnlich wie möglich wird. Wir zeichnen Längsvenen mit einem Stapel, zerdrücken das Werkstück leicht und schicken es zum Trocknen. Kleine Blütenblätter müssen 12-15 Stück gemacht werden.
Der Stielrohling sollte in eine Vase oder Flasche gestellt und gebogen werden, um die Blütenblätter leicht fixieren zu können. Als nächstes kleben Sie die Blütenblätter auf den Kern der Blume. Das Drehen des Werkstücks während des Betriebs wird nicht empfohlen, da die Blume ihre Form verlieren kann. Wenn die erste Charge Blütenblätter fixiert ist, lassen wir die Arbeit trocknen und fahren mit der Herstellung mittelgroßer Blütenblätter fort.
Die Technologie zum Formen mittlerer Blütenblätter unterscheidet sich nicht von der oben beschriebenen, jedoch benötigen Kunststoffe für jedes Werkstück 2-mal mehr. Für die zukünftige Pfingstrose müssen Sie 15-20 mittelgroße Blütenblätter formen.
Der letzte Blick sind große Blütenblätter. Sie müssen mit einem Stapel mit rundem Kopf leicht gewölbt sein, und die Kante sollte wie ein "Herz" sein. Das Relief des Werkstücks wird mit Hilfe einer Form gegeben. Das Blütenblatt ist beidseitig bedruckt. Solche Rohlinge benötigen 10-12 Stück. Fertig getrocknete Blütenblätter werden auf den Stiel geklebt.
Die Blumenschale ist fertig. Jetzt müssen Sie es trocknen lassen. Solange der Kleber und das Plastik nicht vollständig trocken sind, sollte die Blume nicht umgedreht werden.
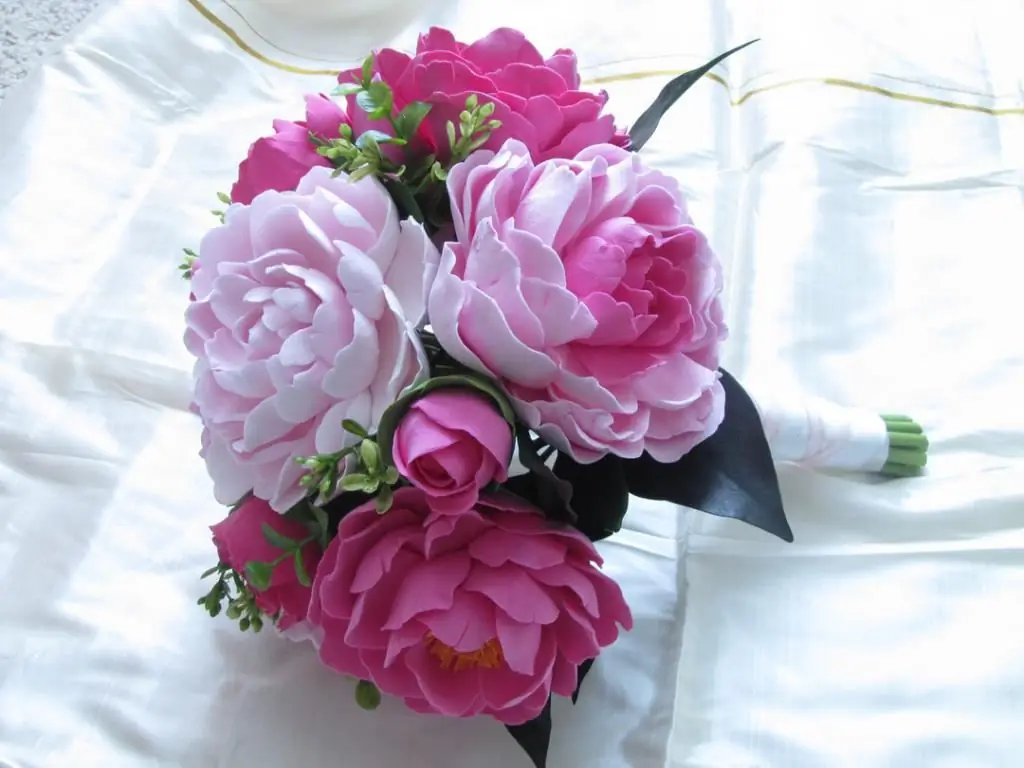
Kelchblatt
Während die Blume trocknet, lass uns die Kelchblätter formen. Sie benötigen 10 Stück: 5 abgerundete konvexe und 5 kleine Blätter. Für die Herstellung vonNehmen Sie vom ersten Typ ein kleines Stück grünen Ton, rollen Sie es aus und geben Sie ihm mit einem Stapel mit rundem Kopf eine konvexe Form. Fügen wir dem Werkstück Textur hinzu, indem wir die Form verwenden, die zum Formen der Blütenblätter verwendet wurde. Lassen Sie uns eine kleine Prise am Rand machen, mit diesem Teil kleben wir das Kelchblatt an die Blume.
Kleine Blätter werden mit einer ähnlichen Technologie wie große Blätter hergestellt. Wir kleben die getrockneten Elemente auf die Blume: Die erste Reihe besteht aus runden Kelchblättern, die zweite aus schmalen Blättern in einem Schachbrettmuster zwischen den runden.
Stamm
Jetzt können Sie den Stamm bearbeiten. Aus grünem Ton machen wir eine 9-11 cm lange Wurst. Wir begradigen den Stammdraht und beschichten ihn mit Klebstoff. Als nächstes bedecken wir den Stiel mit Ton. Wir nivellieren die Nähte und machen den Stiel gleichmäßig dick. Schwer zugängliche Stellen (z. B. neben den Kelchblättern) werden mit einem Stapel mit kleinem Rundkopf geglättet.
Blätter malen
Die Blätter einer echten Pfingstrose haben leicht bräunliche Adern und eine weißliche Unterseite, daher müssen getrocknete Plastikrohlinge bem alt werden, um sie realistisch zu machen. Du brauchst: rote, grüne und weiße Ölfarbe, Pinsel, Verdünner, Papierservietten.
Legen Sie ein Blatt Fimo auf eine Serviette und malen Sie mit einem in Lösungsmittel getauchten Pinsel und dann in Tünche. Verwenden Sie als Nächstes einen trockenen Pinsel, um die Farbe zu mischen. Drehen Sie das Blatt um. Malen Sie mit der gleichen Technologie die andere Seite mit grüner Farbe und schattieren Sie sie. Um die Adern zu zeichnen, mischen Sie Grün- und Rottöne. Wir lassen das Werkstück trocknen. Wir machen die gleichen Operationen mit allen Blättern undKelchblätter.
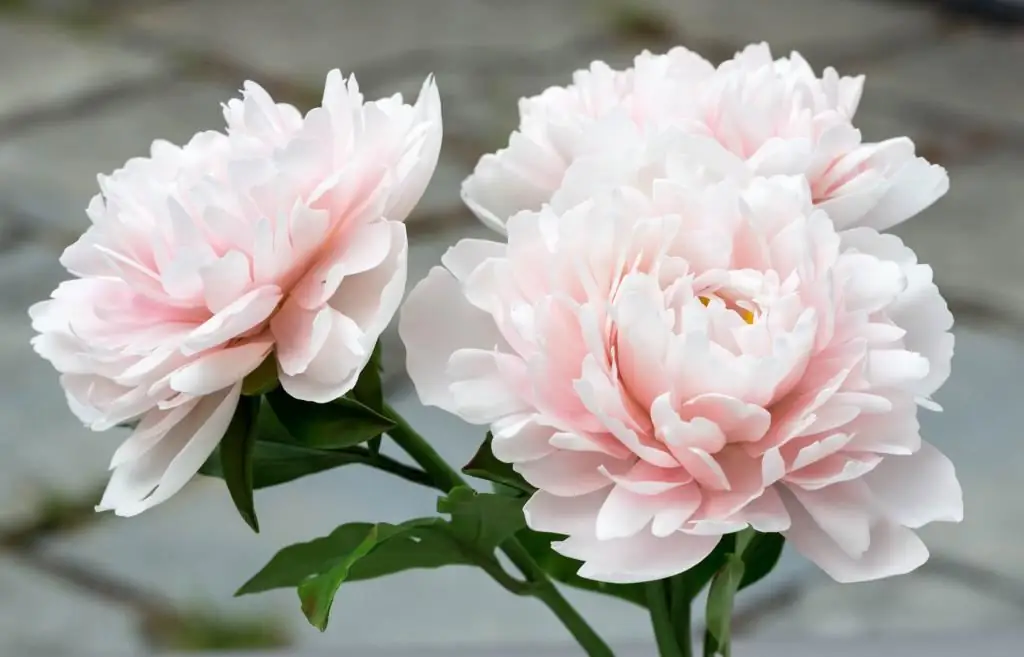
Zweig aufbauen
Nachdem die Blätter trocken sind, können Sie mit dem Zusammenbau des Astes beginnen. Zuerst müssen Sie den Draht teilweise mit grünem Kunststoff umwickeln. Etwa 2 cm von der Blattbasis entfernt. Jetzt können Sie die Fünflinge sammeln. Mit Teiptape wickeln wir einzelne Blätter zum Kleeblatt. Wir fixieren die Enden mit Klebstoff. Als nächstes kleben wir um die Verbindungsstelle und fast den gesamten Draht und lassen einen kleinen Bereich für die Befestigung des Astes am Stamm. Glätten der Nähte. Zweites Fingerkraut zusammenbauen.
In einem Abstand von 10-12 cm von der Knospe befestigen wir den ersten Zweig mit Klebeband am Stiel. Etwas tiefer fixieren wir den zweiten. Bedecken Sie den Stamm und die Fugen mit grünem Lehm, glätten Sie die Fugen und Nähte.
Blumenmalerei
Die Fimo-Pfingstrose ist fast fertig, es bleibt noch, die Blütenblätter leicht zu tönen. Wir beginnen mit dem Kern der Blume. Biegen Sie die Blütenblätter vorsichtig und verwenden Sie einen halbtrockenen Pinsel mit roter Farbe, um die grüne Mitte zu tönen. Als nächstes bemalst du die Ränder einiger Blütenblätter.
Eine elegante Innenblume ist fertig!
Thermoplastischer Schmuck
Aus Plastik werden erstaunlich schöne Schmuckstücke. Ohrringe mit Pfingstrosen aus Polymerton sehen elegant und zart aus. Die Herstellungstechnologie solcher Accessoires ist einerseits einfacher und andererseits schwieriger als Innenfarben. Es ist einfacher, weil die Produkte aus gebranntem Ton hergestellt werden und in der Luft lange plastisch bleiben. Und es ist schwieriger, da die Elemente der Zusammensetzung sehr klein sind und das fertige Produkt einer Wärmebehandlung unterzogen werden muss.
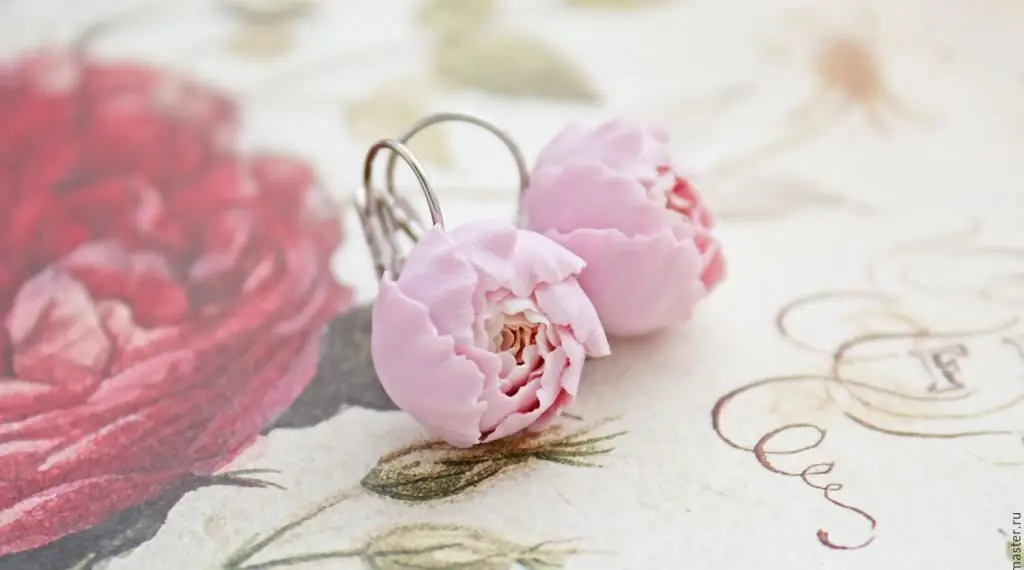
Der Formprozess ist ähnlich dem oben beschriebenen. Als nächstes wird die Blume mit flüssigem Kunststoff in das Loch der Befestigungselemente geklebt. Jetzt muss das Produkt gebacken werden.
Die durchschnittliche Backtemperatur beträgt 110-130 Grad, aber Sie sollten die Anweisungen des Tonherstellers vor der Verwendung sorgfältig studieren. Die Produkte werden auf Pergamentpapier ausgelegt und 10-15 Minuten in den Ofen gestellt. Achten Sie darauf, Fenster zu öffnen, da verdunstende Weichmacher hochgiftig sind. Nach Gebrauch muss der Backofen gründlich mit Spülmittel ausgewaschen werden.
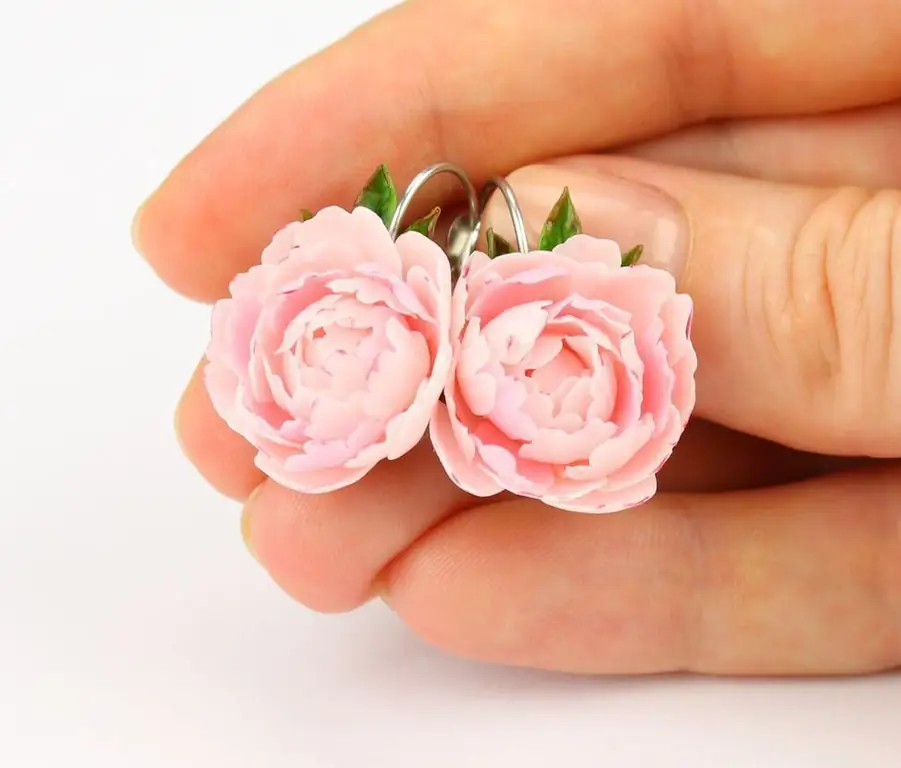
Filigrane Ohrringe sind fertig! Andere Schmuckstücke werden auf die gleiche Weise hergestellt, darunter Broschen mit Pfingstrosen aus Fimo.
Schlussfolgerung
Kunststoff ermöglicht es Ihnen, erstaunlich schöne Innenausstattungen und Accessoires zu kreieren. Blumen aus "k altem Porzellan" verdienen besondere Aufmerksamkeit. Die H altbarkeit und der hohe Realismus der Produkte haben die Herzen von Handwerkern auf der ganzen Welt erobert. Wir hoffen, dass das oben beschriebene detaillierte Pfingstrosen-Tutorial aus Fimo Ihnen dabei hilft, eine wunderbare Komposition für die Dekoration eines Innenraums oder einer Feier zu erstellen.
Empfohlen:
Vorgefertigte Schiffsmodelle zum Selbermachen aus Holz. Beschreibung der Arbeit, Zeichnungen
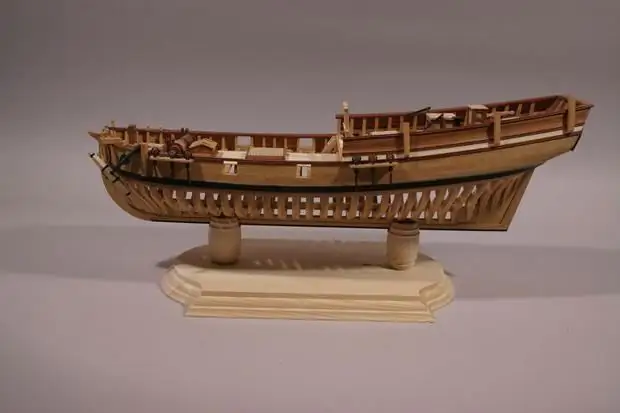
Manche Leute haben ein seltsames, aber sehr bemerkenswertes und buntes Hobby. Schiffsmodelle aus Holz zusammenbauen nennt man das. Was braucht es, um so etwas Schönes zu machen. Es ist nicht so einfach, ein Modell eines Segelschiffs aus Holz zu erstellen. In diesem Artikel erfahren Sie, wie Sie mit Ihren eigenen Händen ein Schiffsmodell aus Holz erstellen. Und wir machen auch einen kleinen Exkurs in die Geschichte
Prinzipien der Arbeit mit der Kamera, die Hauptmodi, die jeder Fotograf braucht: Blendenpriorität und Schärfentiefe
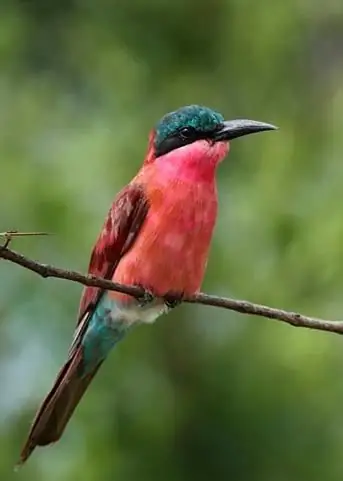
Blendenpriorität ist einer der wichtigsten Modi, den absolut jeder Fotograf, auch Anfänger, verwenden können sollte. Dies ist einer der grundlegenden Modi, die für viele Fotos erforderlich sind
Dekoration der Stickerei in einem Baguette - der letzte Schliff in der Arbeit

Das Sticken eines Bildes ist ein mühsamer, zeitaufwändiger und langwieriger Prozess. Aber das Ergebnis ist ein echtes, von Menschenhand geschaffenes Meisterwerk, das einen anständigen Rahmen braucht. Das Sticken in einem Baguette wird in spezialisierten Werkstätten durchgeführt, dies ist jedoch ein ziemlich teurer Vorgang. Sie können einen Bilderrahmen selbst herstellen
Fimo: wie man es zu Hause macht. Wie man Fimo-Schmuck herstellt
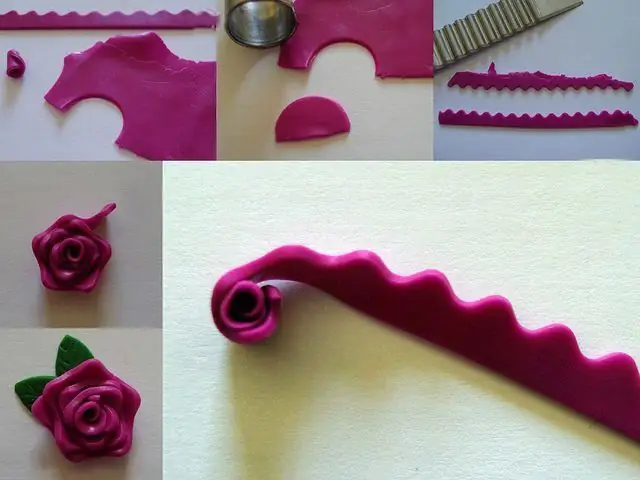
Wenn Sie kein Geld mehr für teuren industriellen Fimo ausgeben möchten, der in Bastelgeschäften verkauft wird, können Sie Ihren eigenen herstellen. Dafür werden einfache Zutaten verwendet, die für jeden verfügbar sind
Eule mit Stricknadeln stricken. Schema und detaillierte Beschreibung der Arbeit

Wer Stricken lernt, beginnt mit der Beherrschung der Technik, dem Erlernen der Grundbegriffe und einem einfachen Anschlag. Dann versuchen sie, den Stoff mit linken und Gesichtsschlaufen zu stricken. Mit dem Erwerb von Erfahrung beherrschen sie das Verflechten von Zöpfen und Zöpfen und gehen dann zu prächtigen Ornamenten und Durchbrüchen über. In diesem Artikel lernen wir, wie man mit Stricknadeln ein sehr schönes und geheimnisvolles Eulenmuster strickt. Das Programm wird in der Stellenbeschreibung angeboten