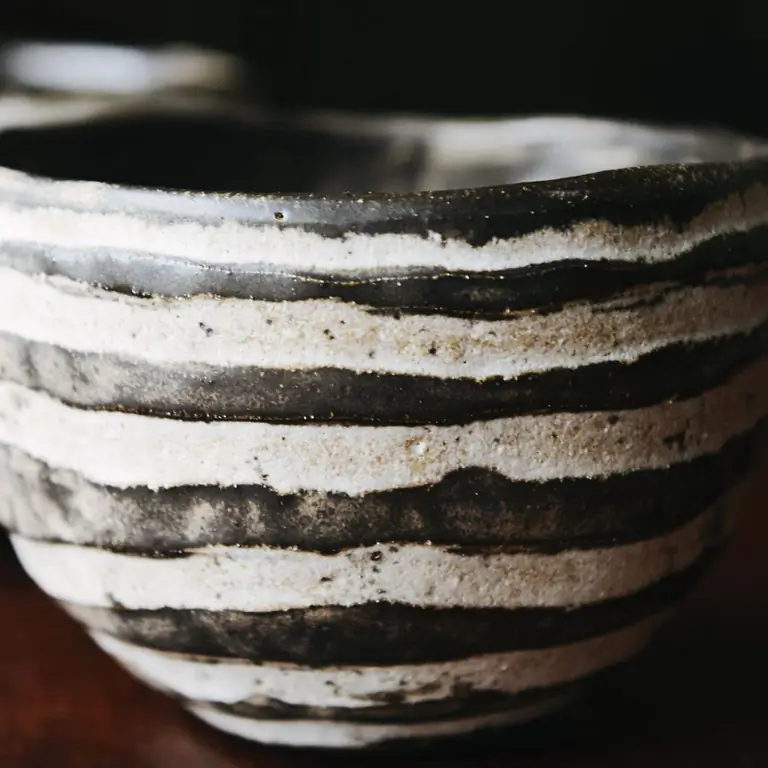
Table of contents:
2025 Author: Sierra Becker | [email protected]. Last modified: 2025-01-22 22:09
Angobe is a white or colored coating for clay products. This substance is ideal for bringing out the natural color of the clay and for adding decorative accents. It is applied to wet or dry clay and then fired. If necessary, it can be covered with glaze. The use of engobe can be traced back to 3000 BC. e. Samples of pottery treated with such a substance were discovered during archaeological excavations.
Engobes for ceramics - what is it
They are a liquid ceramic mass, a mixture of clay, water and, as a rule, a dye. Flux or silica (silicon dioxide) can also be used as ingredients. They are made using fritted material (a frit, a silica-rich glass compound that is fired over low heat until sintered). This reduces shrinkage on the finished product.
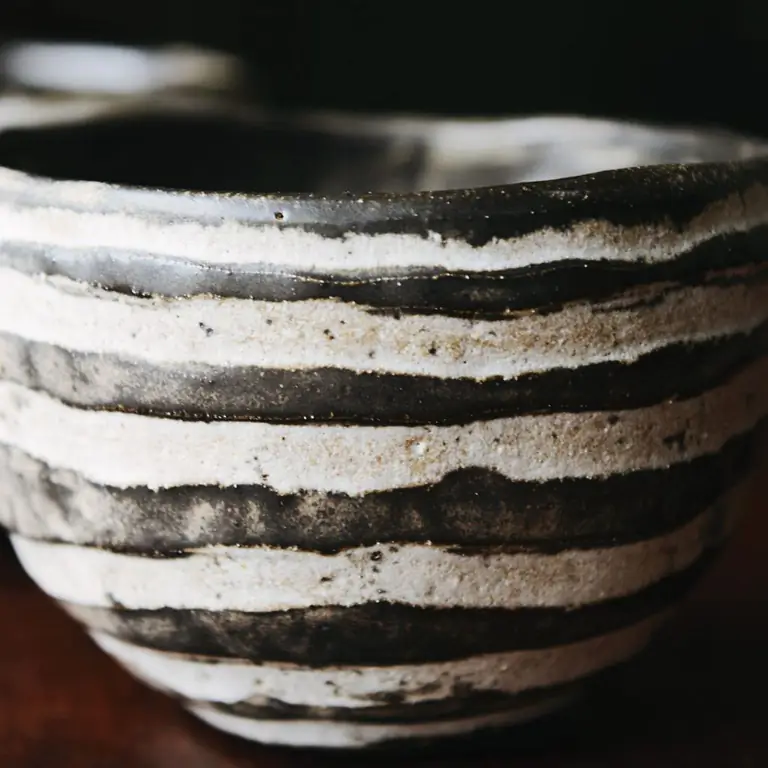
The properties of engobe and glaze are somewhat similar. Glaze isa thin glassy coating used on earthenware. It is a powder mixture of oxides and pigments diluted with water. It is applied by dipping, spraying, watering or brushing. The two finishes differ on the finished product: the glaze has a glossy finish.
How it is used
Angobe is a cover that is considered universal. It is used primarily to give the work depth of color and diversify it.
Colored engobes are used as underglaze paints. They are characterized by great color richness, with their help a rich color palette is easily created with very numerous shades and subtle transitions.
Engobee is one of the most effective ways to color ceramics when using complex, detailed patterns, especially when using several different colors.
It can be used as full or partial cover. It helps to form a smoother surface. Also, with the help of painting with engobes, you can hide unwanted coloring, embossed patterns, and so on. They can be used as a coating, for which no additional processing is used: thus, the product acquires a finished texture and color. It is also used as an intermediate coating between a layer of ceramic and glaze.
Using engobe, you can apply color spots, stripes and complex patterns. For precise drawing, you can use a pencil to mark first. You can also use a stencil.
At the mostengobe is used in the manufacture of tiles as a layer between the base and the glaze. In this case, automated filling / dipping methods are used. The white engobe creates a surface where glazes can have the same vibrant colors as porcelain.
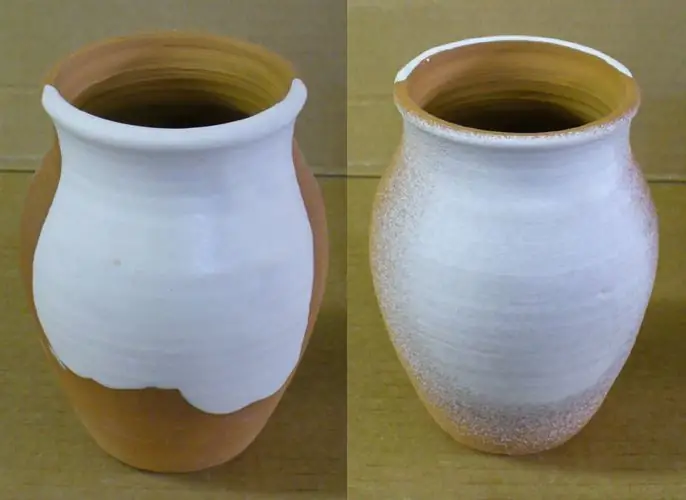
Application
Engobes are applied in the same way as glaze, by watering, dipping, spraying or using a brush. In this case, the product can be raw, slightly dried, dry or pre-fired. After the engobe has been applied, the product can be immediately covered with glaze and sent for firing. However, the greatest effect is achieved if the glaze is applied after the engobe-coated piece has been fired.
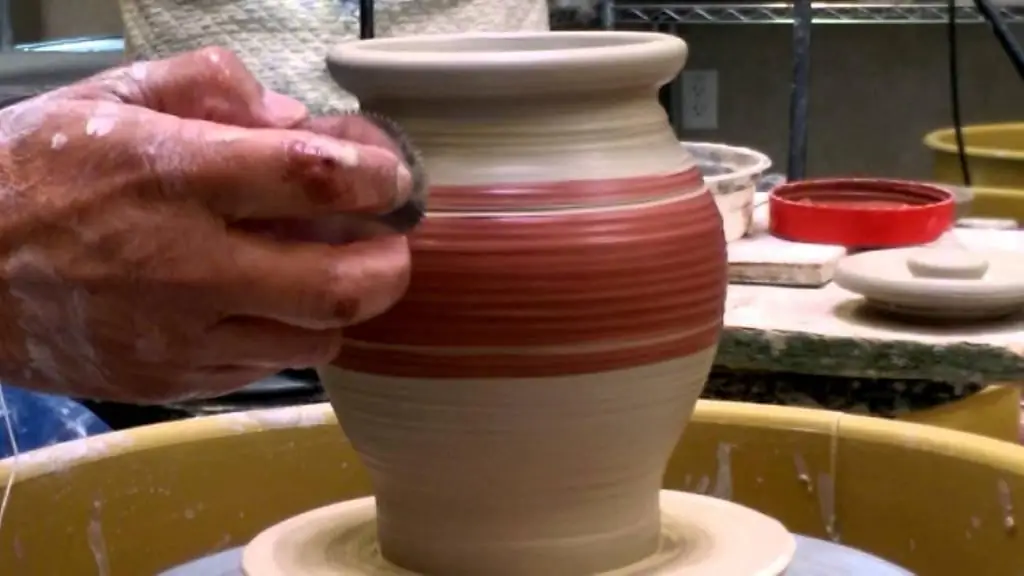
Application conditions
The main conditions for high-quality coating of products with engobe: impeccably clean surface of the product, compliance with the air and fire shrinkage of the engobe and the engobe material, rough surface of the product to ensure sintering of the engobe with the base material. The thickness of the applied engobe layer should not exceed 0.2 mm, since a thicker coating may peel off when dried and fired.
Production
There is a certain technology for preparing engobe. Solid materials (pegmatite, chalk, cullet) are first washed, sorted and crushed. Then they are dosed in accordance with the composition, placed in a ball mill, where 40% water is added to them, as well as, if necessary, coloring pigments. Processgrinding and mixing takes from 20 to 25 hours, after which the resulting mixture is filtered and poured into containers.
Tobacco engobe
For the first time this technique appeared in England quite by accident, when the craftsman spat chewing tobacco onto the item being decorated, as a result of which drawings similar to branches or corals began to spread.
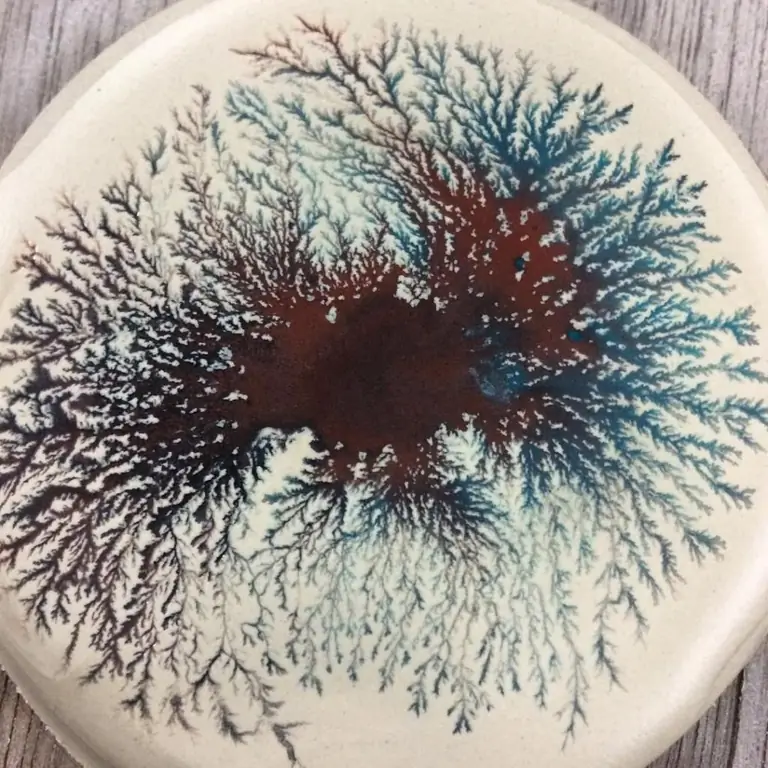
Black engobe is diluted to a slightly thinner consistency than usual. Tobacco pomace is added to it. You can also use engobe of any color with the addition of pigment or oxide. In this case, the process occurs by mixing acidic and alkaline media. The first one can be crafted with vinegar, citric acid, turpentine, faerie, and even beer.
In order to apply a drawing, it is necessary to drip the resulting mixture without touching the product with a brush. After that, the product is dried, fired, covered with a transparent or translucent glaze and fired again.
Features of the creation process
Improving the rheology (flowability of a substance), taking into account the specific gravity, viscosity and thixotropy (ability to thin) of a suspension, is a complex, delicate process. Great importance is attached to the equipment for mixing, since it is necessary to ensure that no air bubbles are drawn into the mass during the process. For quick drying of the engobe, not too large a specific gravity of the base is required, a sufficient amount of liquid to ensure fluidity and viscosity. The consistency of engobe changes during storage, so it is necessary to mix and adjust thoroughlydegree of viscosity with each use.
When using it, remember that the thicker the layer, the more problems it creates. When applied to solid products, the engobe must mechanically bond to the surface during drying and shrinkage. When a glaze is applied to an engobe, it is important that the thermal expansions of the two materials complement each other.
In each case, the shrinkage ratio of the engobe is an important parameter, it must match that of the clay underneath, otherwise the top layer will be damaged.
Materials to create
They are divided into several groups:
- clays with kaolin or calcined kaolin, commonly used instead of ball clay to resist shrinkage;
- fluxes used in glaze;
- fillers (usually silicon dioxide);
- hardeners (borax, calcium borate and various resins)
- dyes.
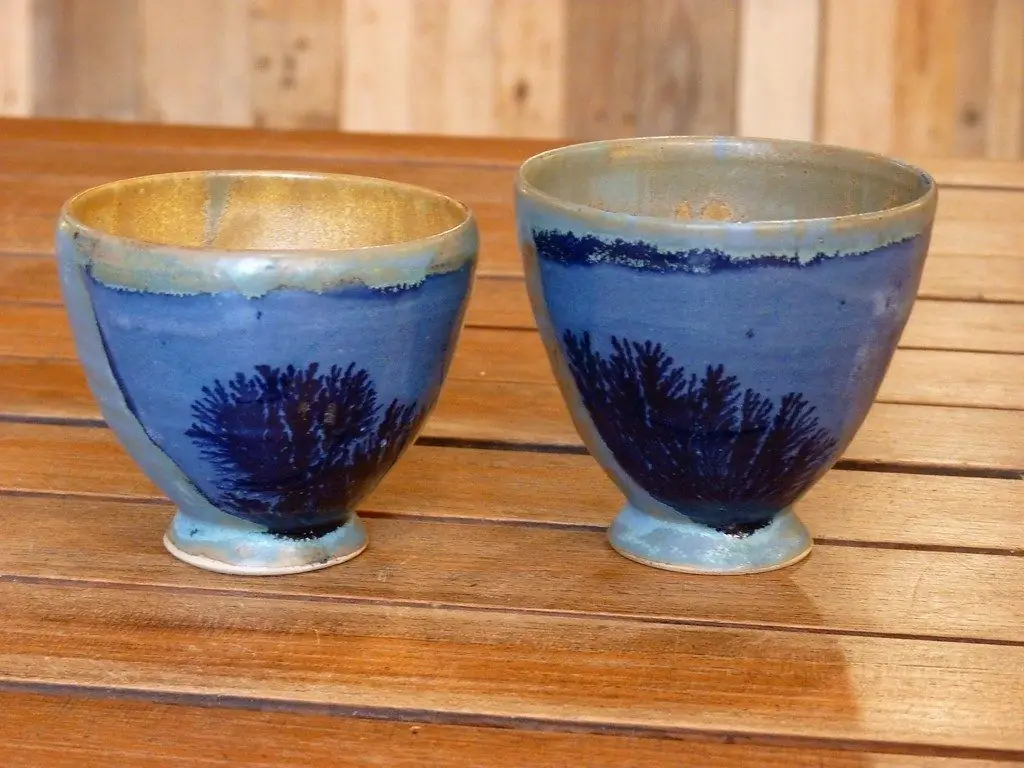
Basic engobe recipes
The following three basic engobe recipes provide a good starting point for further experimentation. Engobes can be dyed in any conventional way.
It may include components in the following percentage:
- Kaolin - 20, talc - 25, calcined kaolin - 10, calcium borate - 15, silicon dioxide - 15, borax - 5, circopax - 10.
- Kaolin - 15, talc - 10, calcined kaolin - 20, calcium borate - 10, nepheline syenite - 10, borax - 5, silicon dioxide - 20, circopax (zircon opacifier for glazes) - 10.
- Kaolin - 15, talc - 5, calcined kaolin - 35, nepheline syenite - 15, borax - 5, silicon dioxide - 15, circopax - 10.
Getting color engobe
When making a colored engobe, a carefully measured amount of coloring pigment is taken. First, it is ground on glass with the addition of water. Then the white engobe is thoroughly mixed with the resulting mass until it is evenly colored.
You can use 40% ball clay, 20% red iron oxide, 20% manganese dioxide, 20% cob alt oxide to create a simple blue engobe.
A variety of oxides, carbonates and commercial dyes can be used to color basic engobe recipes. Some colors can be obtained by adding the following dyes.
Black tint is obtained by adding 3% iron oxide and 2% each of cob alt oxide, nickel oxide, manganese dioxide.
Dark blue color is achieved by adding 1.5% cob alt oxide.
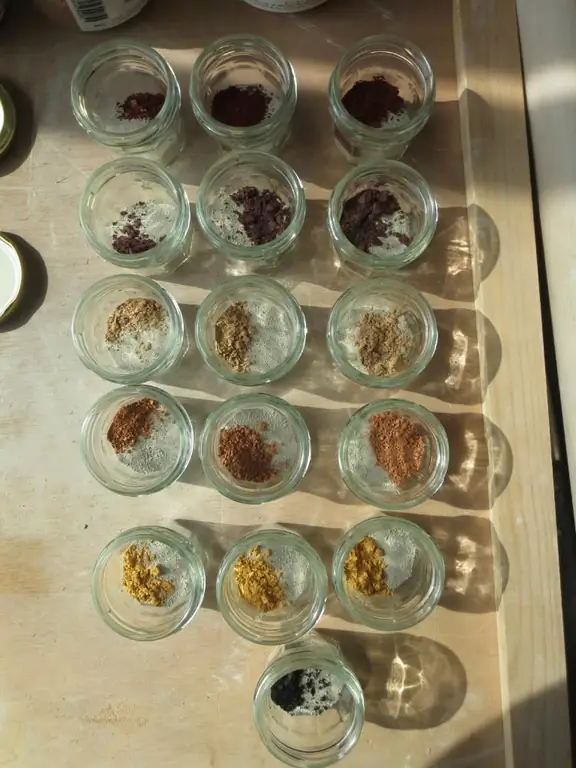
Medium green color obtained by adding 3% copper oxide.
Ocher is obtained by adding 4.5% yellow ocher.
Medium red color achieved by adding 3% iron oxide.
When adding 6% rutile, a creamy brown shade can be achieved.
If you add 3% iron chromate, you get a dark gray engobe. Adding 6% manganese dioxide will result in a purple-brown color.
Recommended:
Knitted fabric: type and quality of material, structure, purpose and application

Knitting sweaters, dresses and blankets takes a lot of time, and there is no guarantee that the first time you will be able to make all the loops the same, and the details will match the pattern. It is in such cases that a finished knitted fabric is used. Using this material, the time to create a product is significantly reduced, however, there are several features of working with it
Stripe satin: what is this fabric, composition, description, application, advantages and disadvantages
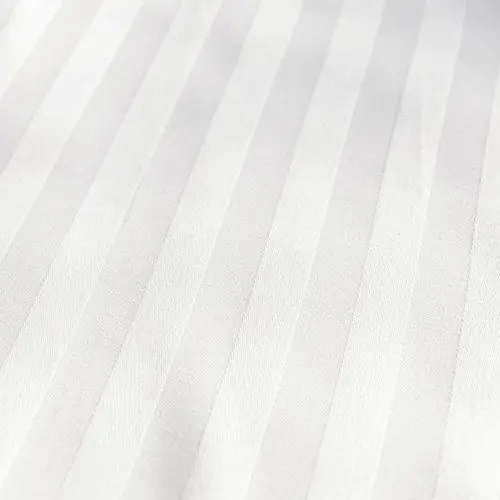
Satin stripe: what kind of material? What is it made from. Production technology. Features, advantages and disadvantages of stripe satin. What is made from this material. Basic rules for the care of stripe satin products
Types of application. Decorative application: master class
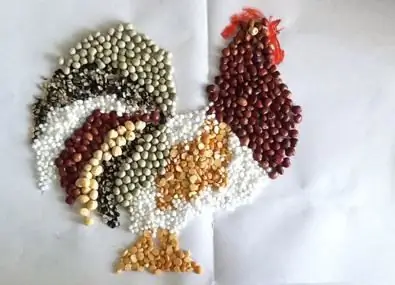
In translation from Latin, the word "application" means "attachment". To make a picture using this technique, you need to cut out various shapes from the same material and attach them to the base, which is the background. For work, you can use paper, cloth, cereal and many other improvised means. Let's take a closer look at what types of applications are and what are the features of their creation
Rusty varnish: composition and application
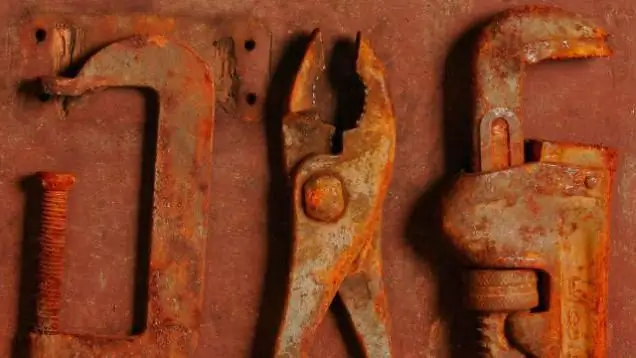
We have all experienced rust more than once, it follows us everywhere, it can be found both on fences, locks, chains located on the street, and on items that we store at home, for example: on knives, keys, reenactment swords and on gun barrels
Original application of seeds and cereals: features and ideas
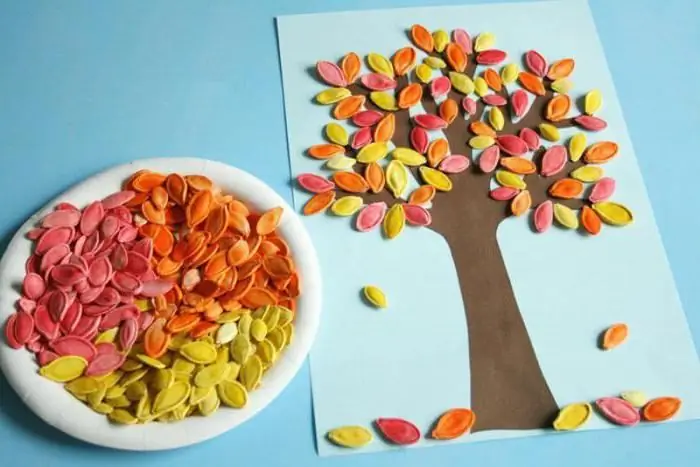
Don't know what to do on an autumn evening? Seed application will be an excellent solution to this problem. We will not only offer you the main ideas of autumn creativity, but also share all the nuances and difficulties that you may encounter while working with various cereals